Share this
Costs of Manual Labor in Liquid Filling & How Automation Solves Them
by Elliott Burge on Mar 17, 2025
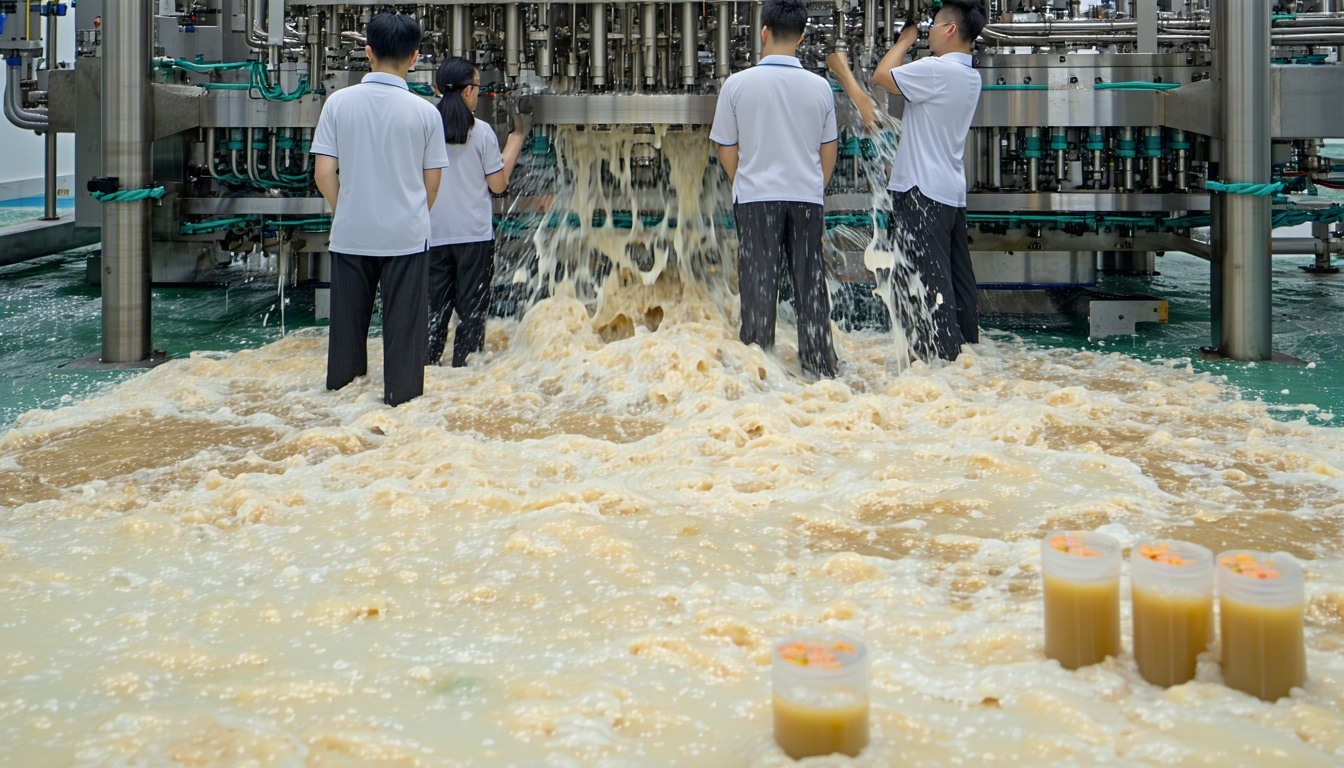
Introduction: The True Cost of Manual Labor
For manufacturers and co-packers in the liquid filling and bottling industry, labor-intensive operations present a significant challenge. Whether it’s rising wages, human error, production inefficiencies, or workplace injuries, relying too heavily on manual labor can lead to increased costs, lost production time, and compliance risks.
Brands today demand speed, consistency, and quality, and if your production line isn’t meeting those expectations, they’ll find a partner who can. The solution? Automated filling, capping, and labeling systems that improve efficiency, reduce waste, and eliminate costly labor inefficiencies.
At Apex Filling Systems, we provide scalable, automated solutions that help manufacturers and co-packers streamline operations, increase profitability, and stay ahead of the competition. Let’s break down the true costs and risks of labor-intensive operations—and how automation solves them.
1. The Rising Cost of Labor & Lost Production Time
With wages, benefits, and turnover rates increasing, labor costs can quickly eat into profits.
- Higher Wages & Payroll Expenses: Salaries, overtime, and benefits increase operational costs. As labor shortages continue, companies are forced to pay higher wages to retain workers.
- Training & Turnover Costs: Hiring and retraining workers leads to inconsistencies in production and increased onboarding expenses.
- Inefficiencies in Changeovers & Adjustments: Manual changeovers take time, delaying production and reducing output. Automated filling and capping solutions allow for rapid, tool-free adjustments, minimizing downtime between product runs.
The Automation Solution:
- Automated production lines eliminate reliance on excessive manual labor, allowing companies to operate efficiently with fewer workers.
- Quick-changeover technology reduces retooling time, allowing co-packers to handle multiple SKUs with ease.
2. Human Error Leads to Product Waste & Inconsistencies
Even the most experienced workers make mistakes. In a manual production environment, errors result in:
- Inconsistent Fill Levels – Overfilling leads to product loss, while underfilling causes compliance issues and customer dissatisfaction.
- Capping Issues – Loose or overtightened caps result in leaks, product spoilage, and safety hazards.
- Misapplied Labels – Poorly placed labels make products look unprofessional, fail to meet branding standards, and risk non-compliance.
The Automation Solution:
- Precision filling equipment ensures exact dosing, eliminating product waste.
- Automated capping machines apply consistent torque, ensuring leak-proof, secure seals.
- High-speed labeling systems apply labels accurately and efficiently, improving packaging quality.
3. Slow Production & Downtime Impact Profitability
Manual bottling and packaging processes are inherently slower than automated systems.
- Production bottlenecks occur when workers struggle to keep pace with demand.
- Breaks, shift changes, and absenteeism create inconsistencies in workflow.
- Manual changeovers take time, delaying product transitions and limiting batch flexibility.
The Automation Solution:
- Automated bottling lines operate continuously, significantly increasing output.
- Programmable controls allow seamless adjustments for different products, eliminating lengthy manual changeovers.
- Integrated systems (filling, capping, and labeling) create a streamlined, efficient process, maximizing production capacity.
4. Safety Risks & Compliance Issues
Manufacturing environments with liquid products present safety hazards. Without proper precautions, companies face:
- Worker Injuries from Repetitive Tasks: Manual bottling, capping, and labeling increase the risk of repetitive strain injuries.
- Chemical Exposure Risks: In industries such as personal care, chemicals, and liquid fertilizers, manual filling exposes workers to hazardous substances.
- Slips & Falls from Spills: Human error in handling liquid products leads to unsafe working conditions.
The Automation Solution:
- Enclosed, automated filling systems prevent direct contact with hazardous materials.
- Automated capping and labeling reduce strain injuries, making operations safer for workers.
- Precision filling technology minimizes spills, reducing workplace hazards.
5. Compliance Risks & Regulatory Penalties
Failing to meet industry standards can result in fines, product recalls, and lost contracts. Manual processes increase the risk of:
- Improper Fill Levels & Labeling Violations – Non-compliant packaging results in fines and regulatory action.
- Tamper-Evident Packaging Failures – Faulty seals or missing induction liners compromise product integrity and consumer trust.
- Cross-Contamination Risks – Improper cleaning between product runs jeopardizes safety standards.
The Automation Solution:
- Automated systems ensure consistent, regulation-compliant fills, capping, and labeling.
- Tamper-evident packaging solutions protect product integrity and meet FDA, USDA, and GMP requirements.
- Sanitary, easy-to-clean equipment ensures compliance with strict industry standards.
Why Automation is the Smart Investment
While manual labor comes with hidden costs, automation delivers measurable savings and efficiency gains.
✅ Lower labor costs – Reduced dependency on manual workers, leading to lower payroll expenses.
✅ Higher production output – Increased speed and accuracy drive greater profitability.
✅ Fewer mistakes, less waste – Precision automation ensures consistent product quality.
✅ Improved workplace safety – Reduces injuries, contamination risks, and liability.
✅ Scalability & future-proofing – Automation allows for seamless growth and expansion into new markets.
At Apex Filling Systems, we provide customized automation solutions to help manufacturers streamline operations, reduce costs, and increase productivity.
Conclusion: The Future of Liquid Bottling is Automated
If your company is struggling with labor inefficiencies, production bottlenecks, or rising costs, now is the time to invest in automation.
The right filling, capping, and labeling systems will:
- Reduce labor dependency
- Increase production speed
- Ensure compliance and quality assurance
- Minimize product waste and downtime
Apex Filling Systems is the trusted partner for manufacturers and co-packers looking to upgrade their bottling operations. Our state-of-the-art automation solutions are designed to boost efficiency, improve quality, and drive profitability.
📞 Contact us today to learn how automation can transform your production line and give you a competitive edge.
🔗 Visit ApexFilling.com to explore our solutions.
Share this
- Help First (78)
- Filling Equipment (30)
- Informational (29)
- Industry Insights (25)
- Apex Filling Systems (23)
- Automatic Filling Machine (22)
- About Apex (19)
- Packaging Equipment (16)
- Apex Filling (9)
- Automatic Capping (9)
- Fillers (9)
- Apex (7)
- Uncategorized (5)
- American Made Goods (2)
- Absolute Truth (1)
- Apex Family (1)
- Apex Way (1)
- Petroleum (1)
- oil (1)
- April 2025 (1)
- March 2025 (10)
- February 2025 (12)
- January 2025 (14)
- December 2024 (1)
- November 2024 (4)
- October 2024 (4)
- September 2024 (2)
- August 2024 (1)
- July 2024 (4)
- October 2022 (1)
- September 2022 (1)
- June 2022 (1)
- October 2021 (2)
- June 2021 (1)
- May 2021 (1)
- April 2021 (2)
- March 2021 (2)
- February 2021 (1)
- January 2021 (2)
- November 2020 (1)
- October 2020 (1)
- September 2020 (2)
- August 2020 (1)
- July 2020 (1)
- June 2020 (1)
- May 2020 (1)
- April 2020 (2)
- March 2020 (2)
- February 2020 (2)
- January 2020 (3)
- December 2019 (2)
- November 2019 (6)
- October 2019 (4)
- September 2019 (3)
- August 2019 (6)
- July 2019 (2)
- April 2019 (1)
- February 2019 (1)
- January 2019 (7)
- December 2018 (6)
- November 2018 (5)
- October 2018 (2)
- September 2018 (2)
- August 2018 (1)
- July 2018 (3)
- May 2018 (2)
- April 2018 (1)
- March 2018 (2)
- February 2018 (2)
- January 2018 (2)