Share this
How to Choose the Right Inline Filling Systems for Your Production Line
by APEX Filling Systems on Nov 25, 2024
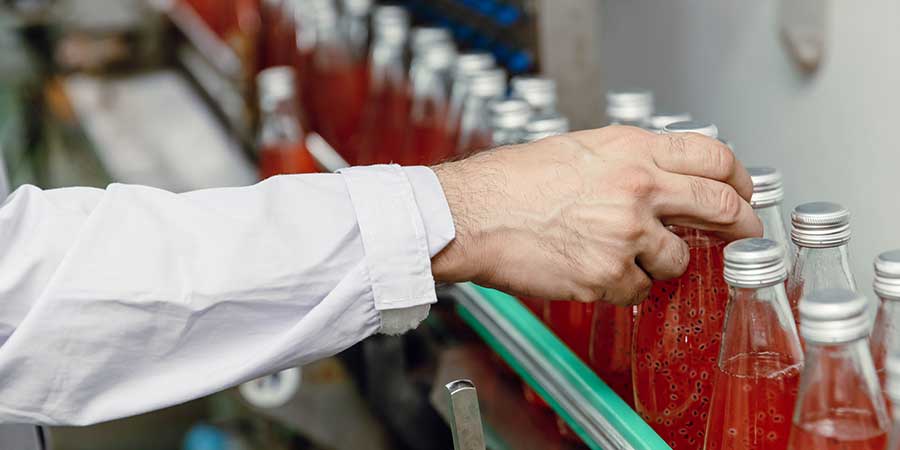
Selecting the right liquid filling machine for your production line is a decision that can make or break the efficiency of your operations. The filling equipment you choose directly affects your output's speed, accuracy, and quality, so getting it right from the start is crucial. A good choice could lead to operational delays, consistent product quality, and unnecessary expenses.
When evaluating your options, start by considering the type of product you’re working with. Different products require different handling, whether thick, viscous liquids or delicate, free-flowing substances. Using the wrong filling system could result in overfills, underfills, or even damage your product.
Production volume is another important factor. Your filling system needs to match the pace of your output without causing slowdowns. If your machine can’t keep up with your production demands, you could face bottlenecks that disrupt your workflow and lead to missed deadlines.
Budget considerations are also key. While it’s important to stay within your financial limits, opting for the cheapest solution can be risky if it doesn’t meet your needs or ends up costing more in maintenance and downtime.
Finally, make sure the new system is compatible with your existing equipment. A system that doesn’t integrate well can cause more harm than good, leading to inefficiencies and additional costs.
Whether upgrading an existing line or setting up a new one, making the right choice will help you maximize productivity and ensure your operations run smoothly.
Understanding Your Liquid Filling Machine Requirements
The liquid-filling technology you use can greatly impact your capacity to meet the demand for your product, regardless of how old or how quickly your business is growing. The right kind of machine must be chosen for your requirements. If you don't know exactly what you need, you can buy equipment that isn't appropriate for your needs, which could cause dissatisfaction and inefficiency.
Here are a few things to consider when selecting the filling equipment ideal for your facility.
Your Product
Start by assessing the viscosity of the products you plan to fill. Viscosity refers to the thickness or fluidity of a liquid, and it plays a significant role in determining which filling technology will work best for your needs.
For instance, thick liquids like sauces or gels may require a piston-filling machine to handle denser materials without causing clogs or inaccuracies. On the other hand, free-flowing liquids like water or juice might be better suited for gravity or pressure fillers, which can operate more quickly and efficiently. Understanding your product's viscosity will help you narrow down your options and choose a filling machine that performs optimally.
Production Volume
Next, consider the container size and shape. Different products are packaged in various containers, from small bottles to large drums, and each container type has its own filling requirements. If you’re working with multiple container sizes, you’ll want an adaptable filling machine that comes with adjustable components.
Some machines offer quick-change features that allow easy switching between different containers, saving valuable time on the production line. Filling speed is another factor to consider. Depending on your production goals, you may need a machine to keep pace with high demand.
Analyze your current production volume and growth projections to determine how fast your filling machine needs to be.
Remember, an efficient machine should consistently deliver precise fills, preventing costly overfills or underfills that can lead to wasted products and dissatisfied customers.
Regulatory requirements
Also, pay attention to the regulatory requirements specific to your industry. Certain products may have strict guidelines that dictate how they must be filled and packaged, especially in sectors like food and pharmaceuticals. Ensuring that your chosen filling machine manufacturer complies with all necessary regulations is vital, as non-compliance can lead to legal issues and potential recalls. Familiarize yourself with the standards that apply to your product type and incorporate them into your decision-making process.
Thoroughly assessing product viscosity, container size, filling speed, and regulatory requirements will help you gain a clearer picture of your needs. This understanding will guide you in selecting a liquid-filling machine that meets your current production demands and supports your future growth and efficiency goals. Evaluating these aspects will set you up for success and help you make a choice that aligns perfectly with your operational needs.
Selecting the Right Liquid Filling Machine Based on Product Type
First, think about your fill rate. How much liquid do you need to bottle daily or monthly? Your answer will guide the automation level for your system. Choosing the right liquid filling machine isn’t just about picking the most advanced or cost-effective option — it’s about understanding how the nature of your product dictates the equipment you need.
Filling machines come in two primary types: semi-automatic and automatic. The distinction between these machines lies in their ability to minimize manual labor, ultimately saving time and enhancing production efficiency in the packaging process.
These industrial filling machine machines are versatile and can be employed across various industries, including food, chemicals, household products, and any sector involved in manufacturing liquid goods. A diverse range of filling machines is available, such as flow meter fillers, piston pump fillers, rotary lobe pump fillers, spiral pump fillers, and gravity fillers. For that reason, you should understand the advantages and limitations of each type and their compatibility with your specific product.
The type of liquid filling solutions also plays a pivotal role. Imagine you’re handling something like a refreshing beverage, delicate perfume, or household cleaner — thin products that flow freely. For these, the filling machine needs to be fast but precise, able to fill each container swiftly without missing a drop. Gravity or overflow fillers are often the answer here. These machines are designed to let the liquid flow naturally, filling each bottle to the same level, which is crucial for maintaining consistency across a large batch.
But what happens when your product isn’t as straightforward? Viscous materials like honey, peanut butter, or lotions present a different challenge. These thicker substances require more force to move through the machinery, where pistons or pump fillers come in. These machines are designed to handle dense, sticky materials, pushing them through the filling process with controlled pressure to ensure each container is filled just right.
And then there are powders. They might seem like a whole different beast, but the fundamentals of filling remain the same: precision and control. Whether you’re packaging spices, protein supplements, or pharmaceuticals, the goal is to handle the product gently yet accurately, ensuring that each package gets the right amount without creating dust clouds or wastage. Here, auger fillers come into play, designed specifically to manage these fine, sometimes tricky, materials.
The size and shape of your containers also matter more than you might think. Filling a tiny vial demands a different machine than filling a large, wide-mouth jar. And don’t forget about the caps — whether they snap, twist, or pump, the capping mechanism must perfectly align with your filling process.
In the end, selecting the right filling machine is about more than just the product — it’s about understanding how it behaves and finding the technology that can handle it efficiently and accurately.
Budgetary Constraints and Compatibility with Existing Equipment With Your Liquid Filling Machine
Of course, the picture is complex, and even machines of the same type can vary in price. As savvy business owners understand, a lower upfront cost doesn’t always translate to long-term savings. A machine that appears economical may become more expensive if it incurs high maintenance costs, experiences frequent downtime, or quickly becomes obsolete.
Several factors influence the overall cost of a filling machine, impacting whether it aligns with your business's long-term financial goals. Regardless of your chosen machine or budget, remember that you might need supplementary equipment, especially if you aim to establish a fully automated production line. Components like conveyors, accumulating tables, and capping machines are crucial for maintaining product flow since a production line's speed is determined by its slowest process.
Just like any investment, the price of filling machines is shaped by various factors that affect the value you receive. Considering the services included in the overall cost is vital, as these can yield significant benefits over time. For instance, manufacturers of higher-priced machines often provide a more extensive support network, ensuring quick maintenance and readily available parts. Although this level of service contributes to the machine's higher price, it can reduce downtime and enhance throughput for your production line.
The degree of automation also plays a crucial role in pricing. Automatic machines generally cost more than their semi-automatic counterparts. A fully automated machine equipped with programmable logic controllers, centralized computer control, sensors, and monitoring systems naturally incurs higher costs. Businesses must evaluate their required level of automation and assess whether the additional investment is justified over time. For many, increased production speeds and lower labor costs can offset the initial investment. Additionally, numerous suppliers offer upgradeable systems, mitigating the investment risk at the outset.
Top Technology Trends and Features in Liquid Filling Solutions
The role of liquid-filling machines has evolved far beyond simply getting the job done. These machines are now at the forefront of technological innovation, designed to make every process step more precise, efficient, and reliable.
Modern machines are built to ensure that every drop counts — literally. When working with liquids, especially in sensitive industries like pharmaceuticals, even a tiny variation can lead to big problems. Today’s filling equipment is engineered to consistently deliver the required amount, minimizing waste and protecting your product’s quality. This level of precision isn’t just about meeting industry standards; it’s about maintaining the trust and satisfaction of your customers.
Automation has also become a game-changer in liquid filling. Imagine a system that speeds up production and keeps everything running smoothly without constant human oversight. Automated systems do just that. They reduce the need for manual labor, reducing the chance of human error. With advanced sensors and real-time monitoring.
Customization is another key feature that’s becoming increasingly valuable. Gone are the days when a one-size-fits-all approach would suffice. Today’s liquid filling machines offer the flexibility to adapt to various products and packaging formats.
But it’s not just about the machines themselves; material compatibility is just as crucial. The equipment you choose needs to work well with the products you’re filling and the packaging you’re using.
Speed is, of course, another essential factor. As production demands grow, so does the need for machines that can keep up without sacrificing accuracy.
High-speed filling machines, like pump fillers, are designed to handle large volumes quickly, making them ideal for industries where time is money. But remember, speed alone isn’t the answer; it’s the balance of speed and precision that truly matters. A machine that’s fast but sloppy won’t do you any favors. The best filling solutions are those that allow you to ramp up production without compromising on the quality of each fill.
Finally, don’t overlook the importance of maintenance and ease of operation. Even the most advanced machines need regular care to perform at their best. Opting for equipment that’s easy to operate and maintain can save you from costly downtime and repairs.
In essence, the top technology trends and features in liquid filling solutions — precision, automation, customization, material compatibility, speed, and ease of maintenance — are all about optimizing your production process.
Making the Right Choice for Your Liquid Filling Needs
Choosing the right liquid filling solution is crucial for the success of your production line. Make an informed decision that aligns with your specific production goals, budget constraints, and technological needs. Each business is unique, and the suitable machine should meet your current requirements and support your future growth.
To help you finalize your choice, here’s a simple decision-making framework:
- Assess your production goals
- Set your budget
- Evaluate automation needs
- Research compatibility
- Consult experts and consider scalability
If you're thinking about investing in a filling machine for your business, we invite you to contact Apex Filling Systems. We prioritize your satisfaction and are committed to exceeding your expectations in every aspect of our service.
Share this
- Help First (78)
- Informational (29)
- Filling Equipment (23)
- Industry Insights (23)
- About Apex (19)
- Automatic Filling Machine (17)
- Apex Filling Systems (16)
- Packaging Equipment (10)
- Apex Filling (8)
- Fillers (8)
- Apex (7)
- Automatic Capping (7)
- Uncategorized (5)
- Absolute Truth (1)
- American Made Goods (1)
- Apex Family (1)
- Apex Way (1)
- February 2025 (12)
- January 2025 (14)
- December 2024 (1)
- November 2024 (4)
- October 2024 (4)
- September 2024 (2)
- August 2024 (1)
- July 2024 (4)
- October 2022 (1)
- September 2022 (1)
- June 2022 (1)
- October 2021 (2)
- June 2021 (1)
- May 2021 (1)
- April 2021 (2)
- March 2021 (2)
- February 2021 (1)
- January 2021 (2)
- November 2020 (1)
- October 2020 (1)
- September 2020 (2)
- August 2020 (1)
- July 2020 (1)
- June 2020 (1)
- May 2020 (1)
- April 2020 (2)
- March 2020 (2)
- February 2020 (2)
- January 2020 (3)
- December 2019 (2)
- November 2019 (6)
- October 2019 (4)
- September 2019 (3)
- August 2019 (6)
- July 2019 (2)
- April 2019 (1)
- February 2019 (1)
- January 2019 (7)
- December 2018 (6)
- November 2018 (5)
- October 2018 (2)
- September 2018 (2)
- August 2018 (1)
- July 2018 (3)
- May 2018 (2)
- April 2018 (1)
- March 2018 (2)
- February 2018 (2)
- January 2018 (2)