Share this
How to Scale Your Production with Modular Liquid Filling Equipment
by APEX Filling Systems on Feb 05, 2025
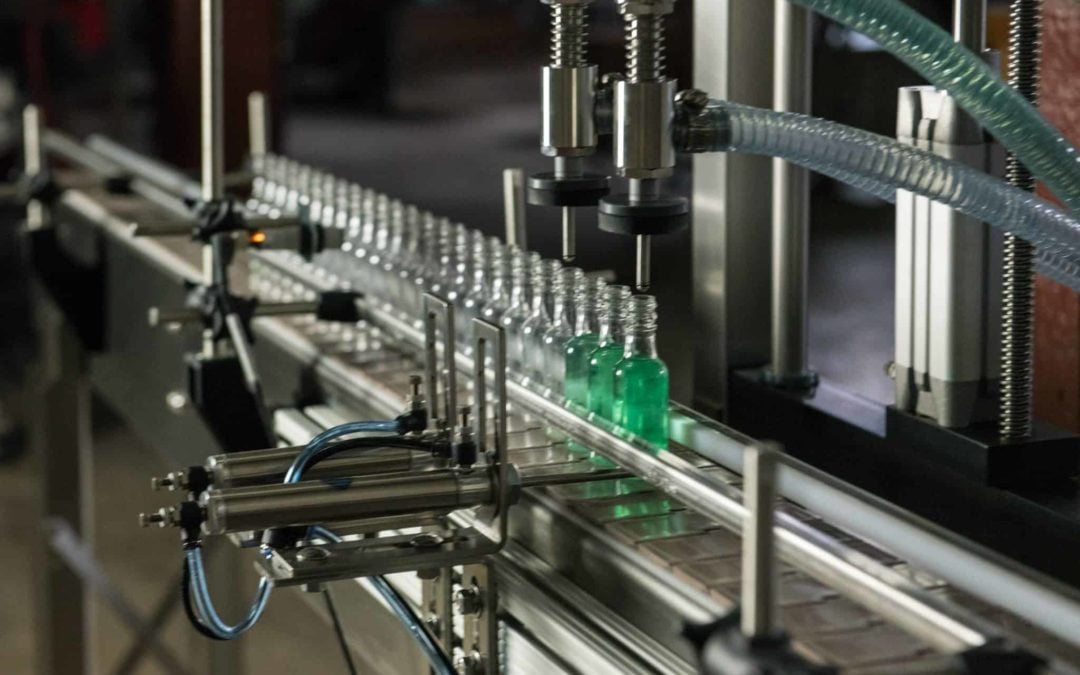
Scaling production is a crucial step for any growing business. As demand increases, the need for flexible, efficient, and scalable production solutions becomes more critical. Modular liquid filling equipment offers manufacturers the ability to expand and optimize their production lines without the costly overhead of fully replacing equipment.
In this blog, we explore the benefits of modular liquid filling solutions, how they adapt to different production needs, and key tips for scaling your operations smoothly and cost-effectively.
What is Modular Liquid Filling Equipment?
Modular filling equipment consists of components that can be easily added, removed, or reconfigured to match a business’s production requirements. Instead of investing in a new system as production scales, manufacturers can upgrade incrementally by integrating new modules like additional filling heads, capping stations, or labeling units.
Core Features of Modular Systems:
- Flexible design: Easily adapt to new products or higher volumes.
- Expandable components: Add more capacity when needed.
- Reduced downtime: Seamlessly upgrade without disrupting production.
Benefits of Modular Liquid Filling Equipment
1. Start Small and Scale Gradually
For small manufacturers or startups, modular systems allow you to begin with a semi-automated or compact setup and expand as production demand grows. As you scale, you can add more features, such as automated conveyors, multi-head fillers, or advanced capping systems.
Example: A small juice manufacturer can start with a basic 2-head filling system and expand to an 8-head setup when production demand increases.
2. Cost Efficiency and Lower Initial Investment
Instead of purchasing an entirely new machine every time you scale, modular systems allow you to upgrade only the necessary components, saving significant costs. For example, you can add new nozzles, filling heads, or automated systems to your existing base unit.
Key Benefit:
- Pay for what you need now, and invest in additional features as your revenue grows.
- Reduce capital expenditures while maximizing ROI.
3. Adapt to New Product Lines with Ease
Modular filling systems can be easily customized to accommodate different types of liquids, viscosities, and packaging formats. Whether you’re introducing a new product or switching container types, modular systems allow for quick and simple reconfigurations.
How It Works:
- Switch between different nozzles for liquids of varying viscosities.
- Adjust the system for different bottle shapes and sizes.
- Add capping or labeling units when expanding product lines.
Example: A cosmetics manufacturer can use the same modular base to fill both thin serums and thick lotions by swapping out appropriate components.
4. Minimize Downtime During Upgrades
With modular systems, you can upgrade without shutting down your entire production line. New components are often plug-and-play, allowing you to install them while keeping the core system operational.
Benefit:
- Maintain production while scaling, reducing downtime and lost revenue.
- Quick integration with existing systems ensures minimal disruptions.
5. Future-Proof Your Production Line
As consumer demand evolves and new technologies emerge, modular systems help you stay ahead of the curve. You can integrate new technologies like AI-powered controls, IoT monitoring, or energy-efficient components into your existing setup without replacing the entire system.
Example: An existing filling system can be upgraded with smart sensors and AI for real-time monitoring, ensuring efficient production and predictive maintenance.
How Modular Liquid Filling Systems Grow with Your Business
Phase 1: Initial Setup for Small-Batch Production
- Semi-automatic systems: Ideal for small batches or startups.
- 2-head or 4-head fillers: Provide enough capacity without overwhelming your budget.
- Manual or semi-automatic capping and labeling: Keep initial costs low.
Phase 2: Expansion as Demand Grows
- Add filling heads to increase production speed.
- Integrate automatic conveyors for continuous production.
- Introduce automatic capping and labeling modules to improve efficiency.
Phase 3: Full Automation for Large-Scale Manufacturing
- Expand to multi-head filling systems for high-speed production.
- Incorporate robotic arms for container handling.
- Utilize AI-powered controls to optimize fill levels and minimize waste.
- Enable remote monitoring with IoT for real-time performance tracking.
Tips for Successfully Scaling Production
-
Choose a Modular System Built for Expansion:
Ensure your initial system has the flexibility to accommodate future upgrades. -
Plan for Long-Term Growth:
Even if you’re starting small, consider your projected growth and select a scalable solution. -
Invest in Operator Training:
As you expand, properly trained operators will maximize the efficiency of your upgraded system. -
Consider Automation in Phases:
Begin with semi-automated processes, and gradually add automated components as needed. -
Monitor Performance Regularly:
Use IoT and machine performance data to identify when scaling is necessary.
FAQs
1. What is the advantage of modular liquid filling systems over traditional systems?
Modular systems allow for incremental upgrades, providing cost-effective scalability and flexibility compared to fixed traditional systems that require full replacement for expansion.
2. Are modular systems only suitable for large manufacturers?
No! Modular systems are perfect for small manufacturers as they allow you to start small and scale without the high upfront cost of large systems.
3. Can modular systems handle multiple product types?
Yes, modular systems are designed to accommodate different products by swapping out components like nozzles, filling heads, and conveyors.
4. How do modular upgrades affect downtime?
Most modular systems feature plug-and-play components, minimizing downtime during upgrades.
Why Choose Apex Filling Systems for Modular Solutions?
At Apex Filling Systems, we offer customizable modular liquid filling equipment designed to grow with your business. Our solutions provide:
✅ Scalable designs: Start with the basics and expand as needed.
✅ Cost-effective upgrades: Add components as your production grows.
✅ Expert support: Get guidance at every stage of growth.
Ready to scale your production? Contact Apex Filling Systems today to explore modular solutions built for growth!
Share this
- Help First (78)
- Filling Equipment (30)
- Informational (29)
- Industry Insights (25)
- Apex Filling Systems (24)
- Automatic Filling Machine (22)
- About Apex (19)
- Packaging Equipment (17)
- Apex Filling (10)
- Automatic Capping (10)
- Fillers (9)
- Apex (7)
- Uncategorized (5)
- American Made Goods (3)
- Absolute Truth (1)
- Apex Family (1)
- Apex Way (1)
- Petroleum (1)
- oil (1)
- April 2025 (3)
- March 2025 (10)
- February 2025 (12)
- January 2025 (14)
- December 2024 (1)
- November 2024 (4)
- October 2024 (4)
- September 2024 (2)
- August 2024 (1)
- July 2024 (4)
- October 2022 (1)
- September 2022 (1)
- June 2022 (1)
- October 2021 (2)
- June 2021 (1)
- May 2021 (1)
- April 2021 (2)
- March 2021 (2)
- February 2021 (1)
- January 2021 (2)
- November 2020 (1)
- October 2020 (1)
- September 2020 (2)
- August 2020 (1)
- July 2020 (1)
- June 2020 (1)
- May 2020 (1)
- April 2020 (2)
- March 2020 (2)
- February 2020 (2)
- January 2020 (3)
- December 2019 (2)
- November 2019 (6)
- October 2019 (4)
- September 2019 (3)
- August 2019 (6)
- July 2019 (2)
- April 2019 (1)
- February 2019 (1)
- January 2019 (7)
- December 2018 (6)
- November 2018 (5)
- October 2018 (2)
- September 2018 (2)
- August 2018 (1)
- July 2018 (3)
- May 2018 (2)
- April 2018 (1)
- March 2018 (2)
- February 2018 (2)
- January 2018 (2)