Share this
The Apex Guide: Loading and Accumulating Rotary Turntables
by Alicia Cannon on Jan 26, 2021
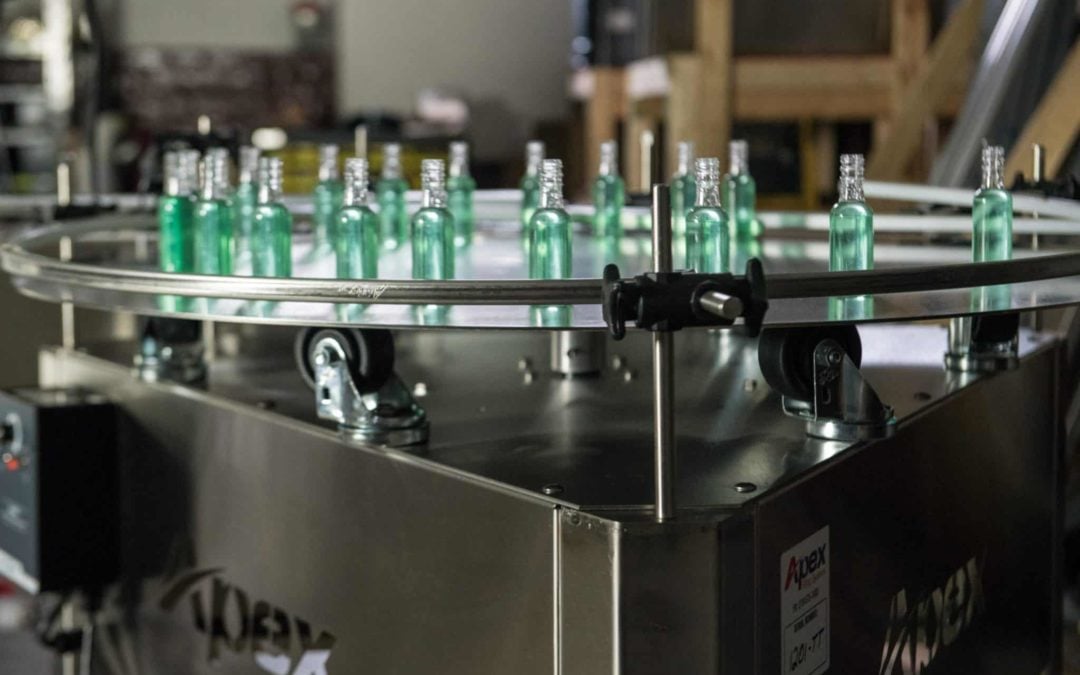
Rotary turntables play an important role in the automation and profitability of the filling process. At higher rates of production, many automated machines only work at peak efficiency when bottles are moved along via a conveyor belt while also being lined up side-to-side with no gaps. For example, a piston filler with multiple heads would miss the bottles that had to be filled and were not positioned precisely. This same careful positioning is also needed for any machine that is designed to handle more than one bottle at a time.
Without a loading rotary turntable, an individual worker would need to constantly load up a long-enough backlog onto the conveyor belt to maintain a steady feed of bottles through whatever machine is being used – such as a filler, capper or labeler. In addition, the bottles would have to be spaced neatly by hand, which would further slow down production. With a loading rotary turntable in place, however, one person can add a large number of containers to the turntable at once and allow the machine to move them evenly onto the conveyor belt. That person can then work on other things in-between reloading the turntable.
Accumulating rotary turntables safely gather up the bottles once they have passed through the machine. Without them, production would have to be stopped frequently before the containers reached the end of the conveyor belt, especially if they are made of fragile materials. The rotating table can also collect many bottles streaming in without the risk of them bunching up and tipping over, as may happen if the conveyor belt ended at a non-rotating tabletop. As the accumulating rotary turntable starts to fill up, the bottles can be removed and packaged while more containers continue to be processed.
Both types of turntables feature stainless steel guide rails and variable speed motors, and they can process up to 150 containers per minute.
Loading the Containers
When the bottles are placed on the loading rotary turntable, the steady rotation of the surface brings them into contact with either the guide rail along the outer edge, or the flexible bottle guide that extends from the center of the disk to nearly the outer edge, forming a narrowing angle. When a batch of containers is too large to fit through the gap between the guide and the rail, the extra bottles either travel around the inner portion of the disc until they are guided by the strip again, or the bottles slightly widen the gap as they pass through it. With repeated rotations, the bottles are soon lined up neatly along the outer edge of the turntable, ready to be moved onto the conveyor belt in single file.
Accumulating Containers at the End of the Line
The process is echoed at the end of the production line as the containers make their way to the accumulating rotary turntable. When the bottles leave the conveyor belt, they pass onto the turntable in a smooth line that goes around the outer edge, held in by the rails. As more bottles come onto the turntable, the movement and the guides work together to move the bottles closer to the center until most of the surface area is filled and the bottles can be removed for packaging or for another stage of the filling process.
These turntables can be an end point of the filling process, or they can hold containers that are being conveyed between two different stages of packaging.
Industry Applications
Turntables are used in the production of cosmetics, food and beverages, cleaning and specialty chemicals, pharmaceuticals, personal care and more.
Features
- Heavy duty 304 stainless steel top
- 304 stainless steel frame
- Variable speed DC motor and controller
- Adjustable bottle guide superstructure
- Stainless steel guide rail with HDPE wear strip
- 34″ height +/- 2″
- Up to 150 containers per minute
- Made in the USA
Customization Options
Additional options include:
- Double rail system
- Additional heights available
- Half moon loading deadplate
- Casters for ease of mobility
- Hazardous location/environment construction – Class I, Division I, Groups C & D
The experts at Apex can help you find the best settings for the size, weight and production demands of your products.
Let Apex Help You
Our team at Apex is available to discuss all aspects of your filling system and advise you on what components would best serve the needs of your company. Call us at 219-575-7493 or visit our page here to discuss the best equipment choices for you.
Alicia Cannon

Integrity, honesty, and a dedication to delivering ambitious results serve as the central themes of Alicia’s career and are evident in every interaction she has with our clients. Her relationship-centered leadership style has paved the way for Apex Filling System’s culture of compassion & empathy, executed with accountability that ensures consistently great outcomes. As a learner for life, her pursuit of continuous personal and professional growth has led Apex Filling Systems to be recognized as an industry innovator in customer experience. Holding advanced degrees in the areas of engineering and management, she has a unique ability to analyze processes, identify potential problems before they arise, and develop standardized solutions to ensure every client of Apex Filling Systems enjoys a hassle-free, professional, and pleasant experience. Her leadership style has been influenced by the work of some of the most well-regarded thought leaders throughout the last 50 years. Among them are Jim Collins, Sally Hogshead, John Maxwell, and Tony Robbins.
Share this
- Help First (78)
- Informational (29)
- Filling Equipment (23)
- Industry Insights (23)
- About Apex (19)
- Automatic Filling Machine (17)
- Apex Filling Systems (16)
- Packaging Equipment (10)
- Apex Filling (8)
- Fillers (8)
- Apex (7)
- Automatic Capping (7)
- Uncategorized (5)
- Absolute Truth (1)
- American Made Goods (1)
- Apex Family (1)
- Apex Way (1)
- February 2025 (12)
- January 2025 (14)
- December 2024 (1)
- November 2024 (4)
- October 2024 (4)
- September 2024 (2)
- August 2024 (1)
- July 2024 (4)
- October 2022 (1)
- September 2022 (1)
- June 2022 (1)
- October 2021 (2)
- June 2021 (1)
- May 2021 (1)
- April 2021 (2)
- March 2021 (2)
- February 2021 (1)
- January 2021 (2)
- November 2020 (1)
- October 2020 (1)
- September 2020 (2)
- August 2020 (1)
- July 2020 (1)
- June 2020 (1)
- May 2020 (1)
- April 2020 (2)
- March 2020 (2)
- February 2020 (2)
- January 2020 (3)
- December 2019 (2)
- November 2019 (6)
- October 2019 (4)
- September 2019 (3)
- August 2019 (6)
- July 2019 (2)
- April 2019 (1)
- February 2019 (1)
- January 2019 (7)
- December 2018 (6)
- November 2018 (5)
- October 2018 (2)
- September 2018 (2)
- August 2018 (1)
- July 2018 (3)
- May 2018 (2)
- April 2018 (1)
- March 2018 (2)
- February 2018 (2)
- January 2018 (2)