Share this
The 7 Key Ways to Finding the Right Liquid Filling Machine
by Alicia Cannon on Jan 10, 2018
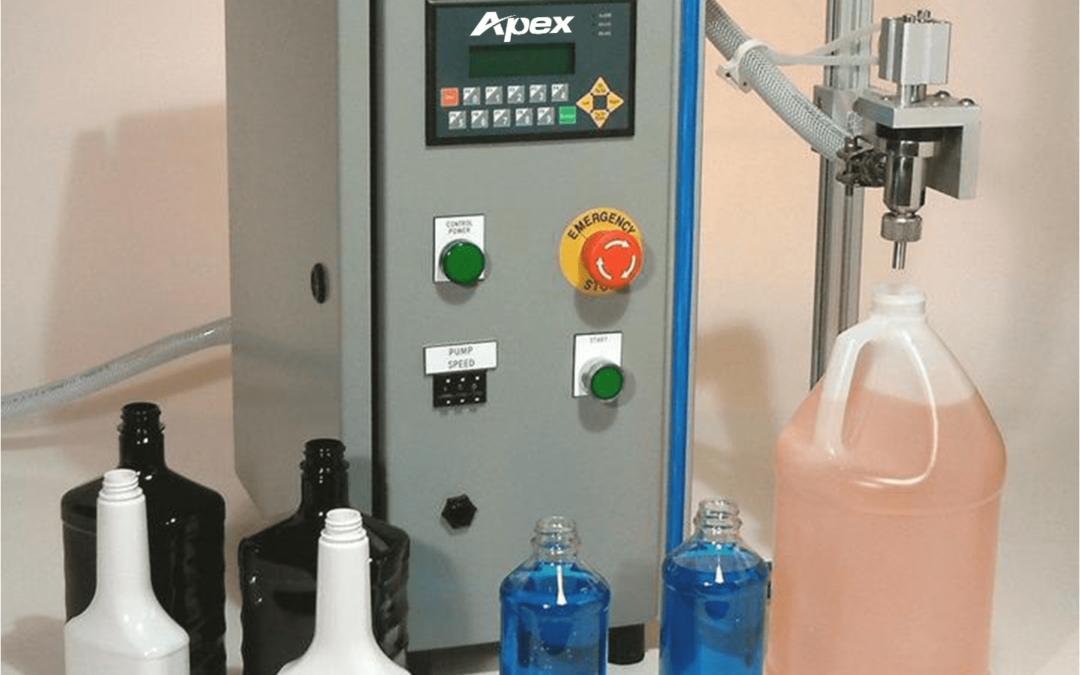
With such a wide range of models and features available today, navigating the liquid filling machine landscape can be a confusing and sometimes overwhelming experience. While there’s no one size fits all solution, we’ve summarized the seven key factors you should consider to help you determine what type of machine best meets your needs.
Whether you’re a home-based craftsperson just beginning to grow your business beyond the hobby stage or a pharmaceutical corporation that packages medicine in precise amounts at the rate of hundreds of bottles per minute, taking a little time to reason through the questions we’ve outlined below will help you make a wise investment.
Liquid Properties: What are the characteristics of your product?
What is its viscosity – the measurement of a fluid’s internal resistance to flow? A substance like molasses will be more resistant to movement than water. As a result, the filling machine you purchase should be able to meet the increased demand of a high viscosity liquid. To get an idea of the viscosity of your liquid, check out our handy Viscosity Table.
Does your product contain particulates? Is it semi-solid? In these instances, a piston or pump filler may be most suitable for the job.
Container: What type will you fill?
What material is it made of? Plastic, glass, or aluminum each require their own specific filling technique. Knowing which material is being used will help determine which filling machine to purchase.
The shape of the container also influences the most appropriate machine. Automatic bottle fillers that grab bottles from the top might not be the best choice if your container has a non-standard lid or cap. In the same way, a bottle filler that grips from the side may not work well with very wide containers. Many bottle filler manufacturers will welcome the chance to review your container and make suggestions for you.
Speed: How fast do you need your bottles filled?
Is faster better? Well, it depends. A business with a very high production rate will likely benefit from the most efficient machines. A smaller business may trade off some speed for savings in cost and space. The speed of smaller machines is measured by bottles produced per hour (BPH). While the speed of larger, more efficient filling machines is measured by bottles per minute (BPM).
One caution: take care to not overlook your future production needs when purchasing your filling machine. It is easier to buy with future growth in mind than to try to upgrade your equipment after the fact.
Automated vs. Manual: What is the appropriate level of automation for your application?
Manual filling machines are meant to handle low production rates, and they are an affordable and space-efficient option for hobbyists or very small companies that do not plan on expanding.
Semi-automatic filling machines can produce bottles at a much faster rate than manual filling machines, but they still require some manual operation. These machines will not reach quite the same speed of fully-automated filling machines. However, their mid-range price often makes them the best choice for small and medium-sized businesses that do not yet need the largest systems, but still have plans to grow.
Automatic filling machines are the powerhouses of production, perfect for large-scale companies with high production rates. These machines pull bottles from bulk storage using conveyors. They require the most floor space, and their purchasing and maintenance costs are higher than for manual or semi-automatic filling machines. However, they function with either no or very little manual operation.
Fill-By Type: Do you need to fill by level or by volume?
A very important decision you need to make is whether a liquid-level filler or a volumetric filling machine is best for your operations. To make this choice, you need to consider two things. What type of liquid you are using and how you want the packaged bottles to appear.
Liquid-level fillers
These fillers fill each bottle to the same specified level, even if the actual volume of liquid varies from bottle to bottle. This method of filling is more efficient and costs less. In addition, it gives all the bottles a uniform, cosmetically-pleasing appearance, which is very appealing to consumers. Liquid level filling machines typically use pressure-overflow fillers, which have a very fast fill rate and can handle a wide range of viscosities. Any leftover product in the filling tubes gets pushed back into the tank, preventing overflow and spillage.
Volumetric filling machines
These machines deliver a precise volume of liquid into each bottle, even when variations in the shape or volume of the bottles may cause the liquids to appear to be at different levels. These types of fillers cost more to operate due to the special instruments they require for timing, calibration and balance. The extra expense is worth it when the liquid needs to be packaged in precise dosages, or when minimizing waste is critical.
Volumetric filling machines are available in three varieties: Gravity-fed fillers which are more cost-effective, and work best with low-viscosity or frothy liquids. The liquid is stored above the bottles as they are filled, allowing gravity to assist in the process. Piston fillers work well with either low-viscosity liquids (check-valve piston fillers) or very thick products (rotary-valve piston fillers). They operate by pumping product from one part of the machine to another in very precise amounts. Finally, pump fillers – while suitable for any viscosity – are especially designed for very thick products that need some extra force to move through the machine.
In-Line vs. Rotary: Is efficiency or flexibility more important for your application?
In-line filling machines fill their bottles in single-file formation, four to twenty bottles at a time. These are a great choice for small or medium-sized businesses. This is because of their lower cost, flexibility in accommodating different bottle shapes, and ease of product change over without the use of change parts.
Rotary filling machines cost more, are more complicated to operate, and cannot be stopped mid-production if any problem arises. In addition, change over takes more time and requires costly change over parts for each unique bottle and cap. Despite this, their high speed and ability to fill over a hundred bottles at once makes them crucial for large business that require high production volumes.
Service and Support: How much customization and support do you need?
Comparing photos of equipment on manufacturers websites can sometimes give you a hint as to their commitment to using quality components. However, it’s most often what you don’t see that distinguishes one manufacturer from another: their commitment to service.
Liquid filling machines are precision pieces of equipment that often represent a significant investment. The best way to maximize that investment is to select a manufacturer who will partner with you to ask pertinent questions, identify your objectives, and design a solution that will consistently exceed your expectations.
When considering manufacturers, always remember to ask about their:
- Ability to customize
- Ability to design turnkey solutions from filling to labeling and everything in between
- Quality review and approval process
- Installation process
- Warranty terms
- On-site support
Finally, never overlook how responsive they are to your inquiries and whether they provide a friendly and professional customer experience. Often, their commitment to the customer experience is closely correlated to their commitment to manufacturing quality equipment that will guarantee your operations are highly productive for years to come.
Naturally, we’d be thrilled to address all of these questions for you and eliminate the guesswork. If you’d like get started today, contact us or just send us your samples.
Best of luck!
Alicia Cannon

Integrity, honesty, and a dedication to delivering ambitious results serve as the central themes of Alicia’s career and are evident in every interaction she has with our clients. Her relationship-centered leadership style has paved the way for Apex Filling System’s culture of compassion & empathy, executed with accountability that ensures consistently great outcomes. As a learner for life, her pursuit of continuous personal and professional growth has led Apex Filling Systems to be recognized as an industry innovator in customer experience. Holding advanced degrees in the areas of engineering and management, she has a unique ability to analyze processes, identify potential problems before they arise, and develop standardized solutions to ensure every client of Apex Filling Systems enjoys a hassle-free, professional, and pleasant experience. Her leadership style has been influenced by the work of some of the most well-regarded thought leaders throughout the last 50 years. Among them are Jim Collins, Sally Hogshead, John Maxwell, and Tony Robbins.
Share this
- Help First (78)
- Filling Equipment (33)
- Informational (31)
- Apex Filling Systems (28)
- Industry Insights (27)
- Automatic Filling Machine (26)
- About Apex (19)
- Packaging Equipment (19)
- Fillers (11)
- Apex Filling (10)
- Automatic Capping (10)
- Apex (7)
- Uncategorized (5)
- American Made Goods (3)
- Apex Family (2)
- Absolute Truth (1)
- Apex Team (1)
- Apex Way (1)
- Petroleum (1)
- oil (1)
- April 2025 (8)
- March 2025 (10)
- February 2025 (12)
- January 2025 (14)
- December 2024 (1)
- November 2024 (4)
- October 2024 (4)
- September 2024 (2)
- August 2024 (1)
- July 2024 (4)
- October 2022 (1)
- September 2022 (1)
- June 2022 (1)
- October 2021 (2)
- June 2021 (1)
- May 2021 (1)
- April 2021 (2)
- March 2021 (2)
- February 2021 (1)
- January 2021 (2)
- November 2020 (1)
- October 2020 (1)
- September 2020 (2)
- August 2020 (1)
- July 2020 (1)
- June 2020 (1)
- May 2020 (1)
- April 2020 (2)
- March 2020 (2)
- February 2020 (2)
- January 2020 (3)
- December 2019 (2)
- November 2019 (6)
- October 2019 (4)
- September 2019 (3)
- August 2019 (6)
- July 2019 (2)
- April 2019 (1)
- February 2019 (1)
- January 2019 (7)
- December 2018 (6)
- November 2018 (5)
- October 2018 (2)
- September 2018 (2)
- August 2018 (1)
- July 2018 (3)
- May 2018 (2)
- April 2018 (1)
- March 2018 (2)
- February 2018 (2)
- January 2018 (2)