Share this
The Apex Guide to: Spindle Cappers
by Alicia Cannon on Sep 22, 2020
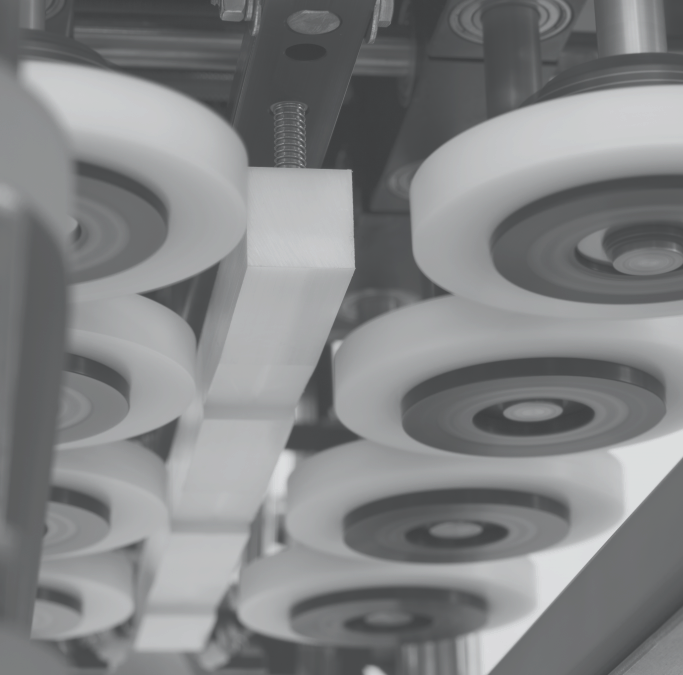
Once your containers have been filled, your products need the protection of a well-sealed cap to prevent contamination and spillage. In many cases, your capping system will also guard your customers from accidental exposure to strong chemicals, and your other inventory will be protected from damage. Adjusting a threaded cap neatly and with the right amount of torque is a painstaking process, but the right capping equipment will do the job efficiently and reliably without causing time-consuming jams or leaks.
The Versatility of Spindle Cappers
Spindle cappers can tighten and torque most types of threaded caps onto most kinds of bottles, and the caps can range in size from 8 mm to 110 mm. The types of caps these machines can handle include:
- flat caps
- oval caps
- flip top caps
- pull spouts
- safety caps
- childproof caps
- sport caps
- caps with over-caps or induction seals
Nearly any type of bottle type or shape can be used, and they can be made from materials that include PET, PP, PVC, HDPE, LDPE and glass. The bottle heights can range from 1” to 14”. Containers with odd shapes can be handled with dual gripper belts.
How They Work
Preparing the caps. Before the capper can receive the bottles, first the caps already have to be set in place. The process can be automated with different optional cap sorting devices: vibratory bowls, which use vertical vibrations to position caps in an energy-efficient way; centrifugal bowls, which place caps into position by means of a spinning motion; or a sorting elevator, where the caps that are correctly placed travel up on a revolving belt, and the ones that are not pop off. The caps can be positioned by hand as the bottles are placed on the conveyer. Depending on the level of automation in place, this can be as easy as emptying a container of caps into a chute.
Holding the parts steady. Just a small misalignment can cause the caps to jam, so the spindle capper has to stabilize both the bottles and the caps as they pass through the spinning disks. This is done with tool-less gripper side belts on both sides of the bottles that keep them upright and in the proper position, and cap stabilizers that put just enough pressure on the caps to keep them from falling off until they are introduced to the tightening process.
Tightening the caps. The capper then tightens the caps onto the bottles using 4, 6 or 8 matched spinning disks (spindle wheels). The bottles go straight through until the correct amount of torque is applied. Depending on the unique configuration of each job, spindle cappers can cap up to 50 bottles per minute.
Easy adjustments: The settings can be adjusted to accommodate different jobs. You can change the torque, spindle wheel position, and gripper belt height and width. The team at Apex is also on hand to help you find the best combination for each capping need.
Industry Applications
Personal care
Nutraceuticals
Cosmetics
Beverages
Pharmaceuticals
Household chemicals
Petroleum products
Features
- Heavy-duty 304SS free standing frame
- Easy integration with most conveyor configurations
- Variable speed SEW AC motors
- 4, 6 or 8 spindle wheels
- Spindle wheel adjustment knobs with locks
- Gripper belt height and width adjustment
- Removable dual gripper belts
- No change parts required for a wide range of containers
- Cap size: 8 mm to 110 mm
- Container height: 1” to 14”
- 304 stainless steel drive shafts and adjustment support shafts
- Adjustable spindle clutches on final set of tightening spindles
- Power height adjustment
- Tool-free changeover
- Made in the USA
Customization Options
We are committed to helping you design the filling system that helps your business succeed.
The modular design of spindle cappers allows you to start with just a cap tightener and easily add automation capabilities such as a chute or automatic cap feeder later as you need them. Additional options include:
- Cap sorting device – vibratory bowl
- Cap sorting device – centrifugal bowl
- Cap sorting device – sorting elevator
- Trigger spray cap rails
- F-style spacer
- Reversible first spindle set (on 8-spindle capper)
- Dual gripper belts
- Hazardous location/environment construction – Class I, Division II, Groups C&D
The spindle capper can also fit into a comprehensive filling operation that includes filling machines, labelers and conveyance systems.
Let Apex Help You
Apex offers all of our clients customized solutions to their filling needs. Call us at 219-575-7493 or visit our page here to discuss the best equipment choices for you.
Alicia Cannon

Integrity, honesty, and a dedication to delivering ambitious results serve as the central themes of Alicia’s career and are evident in every interaction she has with our clients. Her relationship-centered leadership style has paved the way for Apex Filling System’s culture of compassion & empathy, executed with accountability that ensures consistently great outcomes. As a learner for life, her pursuit of continuous personal and professional growth has led Apex Filling Systems to be recognized as an industry innovator in customer experience. Holding advanced degrees in the areas of engineering and management, she has a unique ability to analyze processes, identify potential problems before they arise, and develop standardized solutions to ensure every client of Apex Filling Systems enjoys a hassle-free, professional, and pleasant experience. Her leadership style has been influenced by the work of some of the most well-regarded thought leaders throughout the last 50 years. Among them are Jim Collins, Sally Hogshead, John Maxwell, and Tony Robbins.
Share this
- Help First (78)
- Informational (29)
- Filling Equipment (23)
- Industry Insights (23)
- About Apex (19)
- Automatic Filling Machine (17)
- Apex Filling Systems (16)
- Packaging Equipment (10)
- Apex Filling (8)
- Fillers (8)
- Apex (7)
- Automatic Capping (7)
- Uncategorized (5)
- Absolute Truth (1)
- American Made Goods (1)
- Apex Family (1)
- Apex Way (1)
- February 2025 (12)
- January 2025 (14)
- December 2024 (1)
- November 2024 (4)
- October 2024 (4)
- September 2024 (2)
- August 2024 (1)
- July 2024 (4)
- October 2022 (1)
- September 2022 (1)
- June 2022 (1)
- October 2021 (2)
- June 2021 (1)
- May 2021 (1)
- April 2021 (2)
- March 2021 (2)
- February 2021 (1)
- January 2021 (2)
- November 2020 (1)
- October 2020 (1)
- September 2020 (2)
- August 2020 (1)
- July 2020 (1)
- June 2020 (1)
- May 2020 (1)
- April 2020 (2)
- March 2020 (2)
- February 2020 (2)
- January 2020 (3)
- December 2019 (2)
- November 2019 (6)
- October 2019 (4)
- September 2019 (3)
- August 2019 (6)
- July 2019 (2)
- April 2019 (1)
- February 2019 (1)
- January 2019 (7)
- December 2018 (6)
- November 2018 (5)
- October 2018 (2)
- September 2018 (2)
- August 2018 (1)
- July 2018 (3)
- May 2018 (2)
- April 2018 (1)
- March 2018 (2)
- February 2018 (2)
- January 2018 (2)