Share this
The Hidden Costs of Inefficient Filling Processes (And How to Fix Them)
by Cameron Fehland on Mar 14, 2025
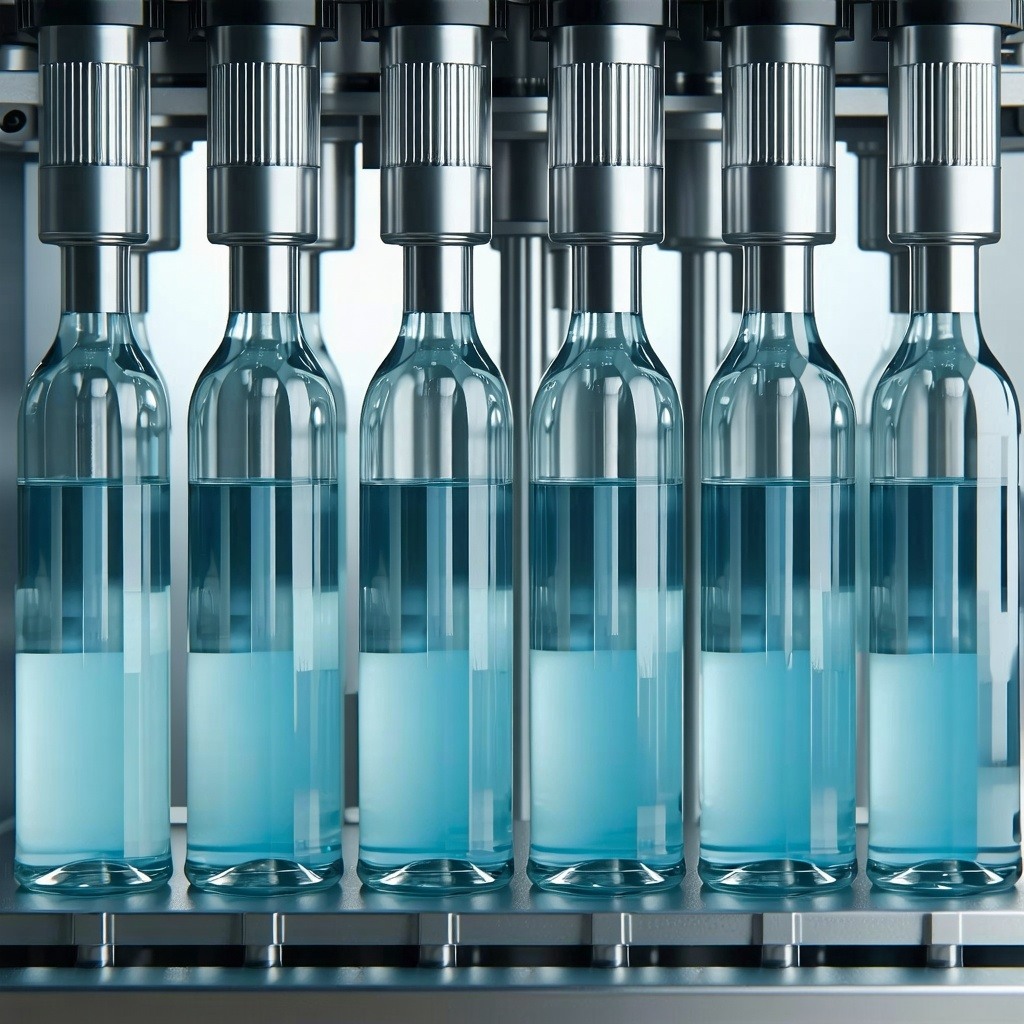
In manufacturing, every second counts. An inefficient filling process can lead to unnecessary costs, wasted product, and lost revenue—issues that often go unnoticed until they start eating into your bottom line. At Apex Filling Systems, we help businesses identify and eliminate these hidden inefficiencies with advanced, reliable, and cost-effective filling solutions.
The True Cost of an Inefficient Filling Process
1. Product Waste
If your filling machine isn’t properly calibrated, you could be dispensing too much or too little product. Overfilling wastes valuable raw materials, while underfilling can result in compliance issues or dissatisfied customers. Even a small overfill per unit adds up over time, significantly increasing production costs.
💡 Fix: Precision-engineered Apex filling machines use advanced controls and automation to ensure consistent fill levels, reducing waste and maximizing profitability.
2. Downtime and Maintenance Costs
Frequent breakdowns and unplanned downtime can bring production to a standstill. Many businesses stick with outdated or poorly maintained equipment, thinking they’re saving money—when in reality, the cost of repairs and lost production time far outweighs the cost of upgrading.
💡 Fix: Apex Filling Systems provides high-quality, durable filling equipment designed for longevity. Regular maintenance and operator training can further reduce downtime and extend machine life.
3. Labor Inefficiencies
Manual or semi-automated filling processes require more manpower, increasing labor costs. If employees spend too much time troubleshooting machine issues or manually adjusting fill levels, productivity suffers.
💡 Fix: Upgrading to a fully automated filling system can significantly reduce labor needs while increasing accuracy and speed. Apex’s user-friendly interfaces and automated features streamline production.
4. Packaging Inconsistencies
Inconsistent fill levels or packaging errors can lead to rejected products, customer complaints, and even regulatory fines. Poorly filled bottles, cans, or pouches may not meet industry standards, resulting in lost inventory and a damaged reputation.
💡 Fix: Apex Filling Systems offers customizable solutions tailored to different container sizes and product viscosities, ensuring uniformity across all batches.
5. Slow Production Speeds
If your filling line isn’t running at optimal efficiency, you’re producing fewer units per hour than you should be. This leads to missed deadlines, delayed shipments, and dissatisfied customers.
💡 Fix: Our high-speed filling machines are engineered for maximum throughput without sacrificing accuracy. Investing in the right machine for your production scale can dramatically improve output.
How Apex Filling Systems Helps You Eliminate Inefficiencies
At Apex Filling Systems, we specialize in designing and manufacturing efficient, high-performance filling solutions that help businesses cut costs and boost productivity. Whether you need a semi-automatic filler for a growing operation or a fully automated system for high-volume production, we have the right solution.
✅ Precision-engineered equipment to minimize waste
✅ Automated solutions to reduce labor costs
✅ Durable machines that require less maintenance and downtime
✅ Scalable options to grow with your business
Don’t Let Inefficiencies Drain Your Profits—Upgrade Today
If your filling process is costing you more than it should, it’s time to make a change. Contact Apex Filling Systems today to learn how our advanced filling machines can streamline your operations, reduce waste, and increase your bottom line.
📞 Call us at 219-402-0213
📧 Email us at cameron@apexfilling.com
🌐 Visit our website: apexfilling.com
Share this
- Help First (78)
- Filling Equipment (30)
- Informational (29)
- Industry Insights (25)
- Apex Filling Systems (23)
- Automatic Filling Machine (22)
- About Apex (19)
- Packaging Equipment (16)
- Apex Filling (9)
- Automatic Capping (9)
- Fillers (9)
- Apex (7)
- Uncategorized (5)
- American Made Goods (2)
- Absolute Truth (1)
- Apex Family (1)
- Apex Way (1)
- Petroleum (1)
- oil (1)
- April 2025 (1)
- March 2025 (10)
- February 2025 (12)
- January 2025 (14)
- December 2024 (1)
- November 2024 (4)
- October 2024 (4)
- September 2024 (2)
- August 2024 (1)
- July 2024 (4)
- October 2022 (1)
- September 2022 (1)
- June 2022 (1)
- October 2021 (2)
- June 2021 (1)
- May 2021 (1)
- April 2021 (2)
- March 2021 (2)
- February 2021 (1)
- January 2021 (2)
- November 2020 (1)
- October 2020 (1)
- September 2020 (2)
- August 2020 (1)
- July 2020 (1)
- June 2020 (1)
- May 2020 (1)
- April 2020 (2)
- March 2020 (2)
- February 2020 (2)
- January 2020 (3)
- December 2019 (2)
- November 2019 (6)
- October 2019 (4)
- September 2019 (3)
- August 2019 (6)
- July 2019 (2)
- April 2019 (1)
- February 2019 (1)
- January 2019 (7)
- December 2018 (6)
- November 2018 (5)
- October 2018 (2)
- September 2018 (2)
- August 2018 (1)
- July 2018 (3)
- May 2018 (2)
- April 2018 (1)
- March 2018 (2)
- February 2018 (2)
- January 2018 (2)