Share this
Automatic Filling Machine Uses: How Different Industries Benefit
by APEX Filling Systems on Sep 09, 2024
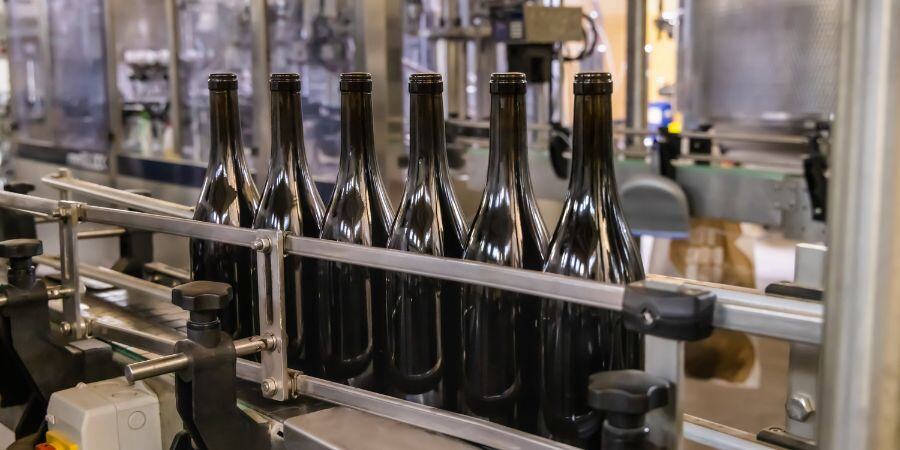
Automatic filling machines have been a true game changer for those who have made the transition from the manual filling process. Industries from cosmetics and pharmaceuticals to the food and beverage industries have always grappled with the challenge of portioning their products into containers for sale to consumers. Manual filling processes have always presented an array of problems for product manufacturing and packaging teams.
Over-filled or under-filled containers, material spills, and contaminated products are all persistent challenges on manual product filling lines. Spills and inaccurate measurements waste valuable resources, drive up costs, slow down production, and often result in subpar-quality products for the end consumer. Automatic filling equipment takes the potential for human error and inconsistency out of the equation, delivering increased speed, boosted productivity, and reduced costs.
The Most Common Manufacturing Challenges
There was a time when the manual filling process was the norm. This was the standard used by most small to mid-sized manufacturers. At that stage, all industries were experiencing roughly the same burdens and resulting costs. This equity of profit & loss made it possible to view even the most costly waste and downtime as a baked-in cost.
Today, business owners have options. Those who choose to modernize will incur an initial expense, but will quickly pull ahead of their former competitors who choose to stick with the status quo. The newest models are being created with a smaller footprint and a lower price point, making it increasingly likely that automated filling systems will be the standard processing method in most factories soon.
Inconsistent Performance
The manual filling process often needs to be more consistent. Humans are not precision-calibrated machinery. They are subject to changes in alertness and accuracy due to any number of causes, from overwork, poor sleep habits, personal stress, and aging. What’s more, one individual rarely fills all the containers. Each new individual introduces additional layers of variability to the process. With multiple workers managing the filling process, the natural variability in performance makes it difficult to produce a uniform product with no waste.
In contrast, automatic filling equipment always gets energized, relaxed, and focused. It delivers an identical amount of product into each container over and over again with no need for breaks. Automated filling equipment will work around the clock without needing rest or overtime pay. You can rest assured that the last product pour will be identical to the first, no matter how long the automated filling equipment has been working.
Wasted Resources
The inconsistency of the manual filling process is not just inefficient, it is inevitably wasteful. Overfilled containers are often unusable and both the container and the product must be tossed in the waste pile. Underfilled products may use less product, however, if the package slips through quality control checks and makes it out to the consumer, the cost to the brand’s reputation could be far higher than the cost of a wasted product. In the best-case scenario, the brand will need to issue a full refund for the underfilled product. The brand will usually need to offer significant quantities of free products to avoid losing a customer and being blasted on the internet by an unhappy customer.
The precise measurement and uniform delivery system employed by automatic filling equipment guarantees that every container is filled with the same volume of product from the first container to the last. No more spilled products, or products and containers that must be thrown away. No need to do damage control with refunded profits and promises of free products.
High Operating Costs
Even the most skilled human laborer will experience mental and physical fatigue within a relatively short period when performing repetitive tasks. This means that factory owners must employ many individual manual fillers to keep the work within manageable limits for human workers. The need for multiple workers makes labor costs one of the largest expenses most business owners face. Human workers are also prone to injury when performing repetitive tasks for a prolonged period. The resulting health care, paid leave, and potential worker compensation claims drive the manufacturer’s costs even higher.
Most factory owners find that the upfront cost of transitioning from manual filling processes to an automated line is easily offset by the reduction of capital currently being allocated to wages, benefits, training, and other expenses associated with employing human laborers.
The Solution: Automated Filling Equipment
Automated filling equipment has completely altered the profitability and growth potential of many industries from pharmaceuticals, and cosmetics to beverage and food retailers. The machines’ ability to deliver consistent precision measurement product pours for any size of run of products significantly increases a factory’s production output, reduces or eliminates waste, and cuts labor costs down to the bare minimum. Taken together, the transformative power of automated filling equipment is clear.
Automated Systems Improve Product Quality and Safety
The unmatched accuracy of automated filling equipment eliminates the quality control issues caused by human error. The machines are calibrated to dispense a precise amount of product in every container ensuring the consumer always receives a full product with the volume shown on the label. The ability to produce consistent quality is even more valuable in the pharmaceutical industry where accurate measurement and blending during the manufacturing and packaging process can have a direct impact on product efficacy. As a bonus, most automated filling systems feature built-in sanitation capabilities as well, allowing for clean, contaminant-free packaging for every product.
Automated Systems Drive Operational Efficiency
Adopting automated filling equipment leads to significant improvements in operational efficiency, reduces costs, and ultimately ensures that your business is able to stay competitive in the modern manufacturing environment.
Improved Operational Efficiency and Reduced Costs
Implementing automated filling machines drastically enhances your brand’s productivity. These machines can work around the clock, with no breaks, and minimal interaction with human operators. They can deliver consistent, high-quality output at a much faster pace than human laborers, increasing overall productivity and greatly reducing the cost of production per product.
Increased Competitiveness
Using automated filling equipment also boosts your competitive edge. By streamlining operations, you can quickly respond to market demands and maintain higher production standards. This equipment allows you to standardize processes, leading to greater product consistency,
How Automatic Filling Equipment Is Used In Various Industries
Cosmetics filling equipment is available in several models, each specially suited to a specific type of cosmetic or beauty product. There are flexible fillers capable of dispensing everything from watery liquids to viscous gels, and textured substances. Fully automatic gravity-feed fillers are capable of accurately dispensing thin liquids into bottles with no human interaction required. Overflow jar filling equipment handles thin to medium viscosity liquid products, including products that are “foamy” by nature. These models are equally well-suited for filling bottles of cleaning chemicals.
Food manufacturers and pharmaceutical makers like the semi-automatic tabletop piston filler for its large hopper that allows for mixing thicker liquids and viscous condiments, sauces, and salsas.
Modernizing your factory with the latest automated filling equipment can significantly boost your business growth potential and ultimately increase your profitability. Embracing innovation can streamline your production processes, making them more efficient and precise.
Automated filling equipment not only boosts operational efficiency, but it sends a message to your staff, and consumers that your business is at the cutting edge and a leader in your industry. Staying ahead of the curve with advanced technology can drive growth and ensure long-term success in increasingly competitive markets.
Ready to Modernize Your Manufacturing Process?
The transition to an automated filling process can provide a massive boost to your business productivity and bottom line. These machines are able to consistently deliver precise amounts of product into any size or style container at a speed that far outpaces manual filling options. Automation eliminates lost time and wasted materials, making it the most cost-effective solution.
With more and more factories modernizing every day, making the switch to automated filling equipment is quickly becoming a necessity for businesses that want to stay competitive in a demanding market. The experts at Apex Filling Systens can help guide you through the process of choosing the right automated solutions for your business. Don’t get left behind, contact us for a consultation and start enjoying the benefits of a modern automated production line.
Share this
- Help First (78)
- Filling Equipment (32)
- Informational (29)
- Apex Filling Systems (25)
- Industry Insights (25)
- Automatic Filling Machine (23)
- About Apex (19)
- Packaging Equipment (18)
- Apex Filling (10)
- Automatic Capping (10)
- Fillers (10)
- Apex (7)
- Uncategorized (5)
- American Made Goods (3)
- Apex Family (2)
- Absolute Truth (1)
- Apex Team (1)
- Apex Way (1)
- Petroleum (1)
- oil (1)
- April 2025 (5)
- March 2025 (10)
- February 2025 (12)
- January 2025 (14)
- December 2024 (1)
- November 2024 (4)
- October 2024 (4)
- September 2024 (2)
- August 2024 (1)
- July 2024 (4)
- October 2022 (1)
- September 2022 (1)
- June 2022 (1)
- October 2021 (2)
- June 2021 (1)
- May 2021 (1)
- April 2021 (2)
- March 2021 (2)
- February 2021 (1)
- January 2021 (2)
- November 2020 (1)
- October 2020 (1)
- September 2020 (2)
- August 2020 (1)
- July 2020 (1)
- June 2020 (1)
- May 2020 (1)
- April 2020 (2)
- March 2020 (2)
- February 2020 (2)
- January 2020 (3)
- December 2019 (2)
- November 2019 (6)
- October 2019 (4)
- September 2019 (3)
- August 2019 (6)
- July 2019 (2)
- April 2019 (1)
- February 2019 (1)
- January 2019 (7)
- December 2018 (6)
- November 2018 (5)
- October 2018 (2)
- September 2018 (2)
- August 2018 (1)
- July 2018 (3)
- May 2018 (2)
- April 2018 (1)
- March 2018 (2)
- February 2018 (2)
- January 2018 (2)