Share this
Top 5 Features to Look for in a Modern Liquid Filling System
by APEX Filling Systems on Apr 09, 2025
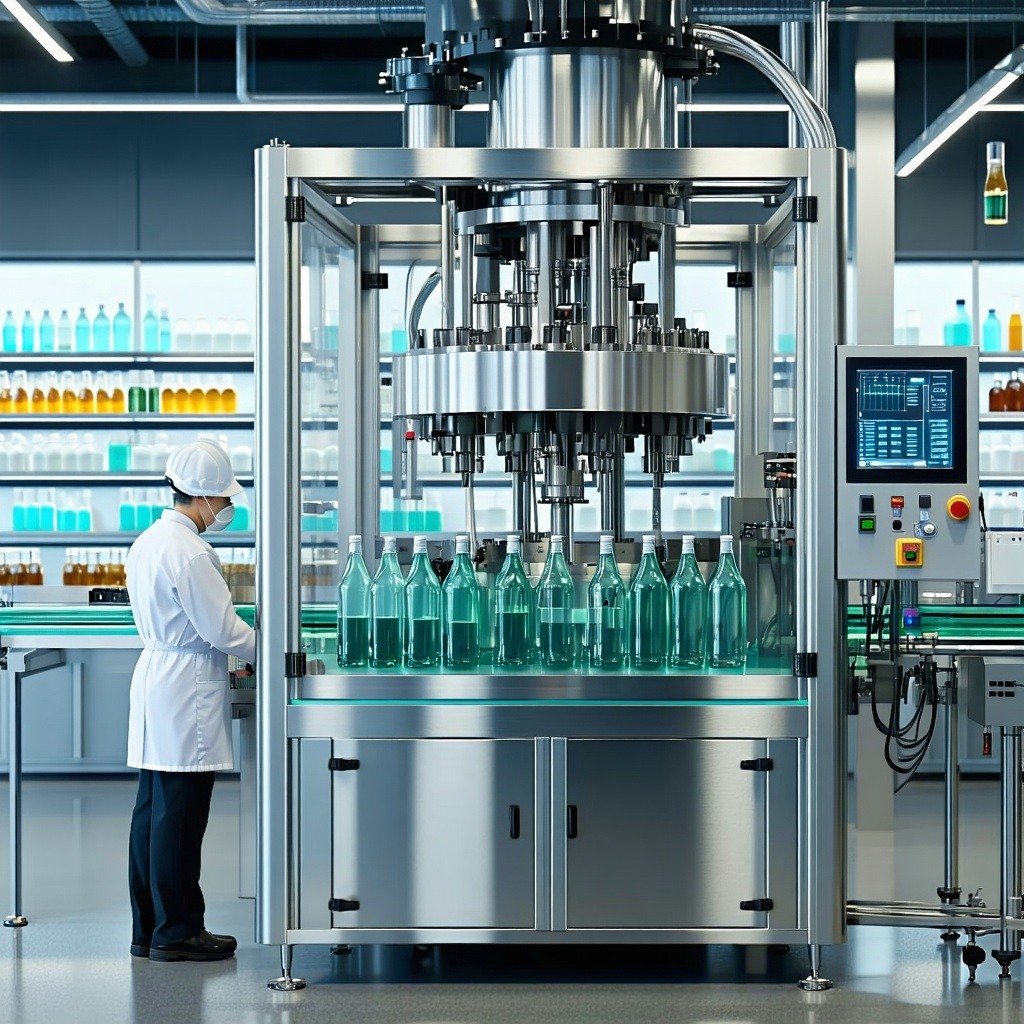
Choosing the right liquid filling system isn’t just about getting product into a container—it’s about doing it with precision, speed, and reliability. Whether you're in the food and beverage, chemical, health and beauty, or pharmaceutical industry, your filling equipment must keep up with modern demands while delivering consistent results.
At Apex Filling Systems, we understand that today’s manufacturers need more than just machinery—they need smart, adaptable solutions that support business growth and reduce operational headaches. In this post, we’ll explore the top five must-have features to look for in a modern liquid filling system.
1. Precision and Fill Volume Accuracy
At the heart of every great filling system is its ability to deliver accurate and repeatable fill volumes. Whether you’re filling 2 oz. glass tinctures or 5-gallon pails, inconsistency leads to:
-
Product waste
-
Regulatory issues (especially in food, chemical, and pharma industries)
-
Customer dissatisfaction
Look for:
✅ Machines with volumetric controls like piston or pump fillers
✅ Overflow fillers for consistent visual levels in clear bottles
✅ Servo-driven systems for dynamic, programmable precision
🔹 Apex Advantage: Our systems are engineered to deliver tight tolerance fills with minimal variation, saving product and boosting quality assurance.
2. Efficiency and Throughput Speed
In today’s competitive market, time is money. A modern filling machine should maximize output without sacrificing quality. Look for equipment that supports:
-
High-speed production with minimal downtime
-
Quick container handling
-
Minimal product changeover time
Look for:
✅ Multi-head systems that scale with demand
✅ Modular components for easy upgrades
✅ Integrated capping and labeling options for full-line automation
🔹 Apex Advantage: Our modular filling lines can start as semi-automatic systems and scale up to fully automated lines, keeping pace with your growth.
3. Versatility for Different Products and Containers
Modern businesses are rarely one-product operations. You may be filling:
-
Different viscosities (thin liquids to thick gels)
-
Varying container sizes and shapes
-
Multiple product types within the same shift
Look for:
✅ Interchangeable nozzles and components
✅ Adjustable speed, pressure, and fill volume controls
✅ Easy changeover features for multi-SKU production
🔹 Apex Advantage: Our systems are built to handle a wide range of liquids, foams, and even corrosive chemicals, with options for gravity, piston, pump, and overflow filling.
4. User-Friendly Controls and Training Support
Ease of use is crucial—especially for teams with limited training or a lean staff. Your system should be intuitive, safe, and easy to operate.
Look for:
✅ Touchscreen interfaces with clear controls
✅ Programmable settings for repeat jobs
✅ Minimal operator training requirements
🔹 Apex Advantage: Our systems are designed with simple interfaces and straightforward functionality, and we provide hands-on training so your team can run with confidence from day one.
5. Cleanability and Maintenance Access
Downtime for cleaning or repairs can cripple production. Choose equipment that’s easy to clean and maintain—especially if you're working in regulated environments (like food, beverage, or health & beauty).
Look for:
✅ Tool-less disassembly for cleaning parts
✅ Sanitary construction materials (304/316 stainless steel or HDPE)
✅ CIP (Clean-in-Place) options for minimal manual labor
🔹 Apex Advantage: Our equipment features easy-access parts, corrosion-resistant materials, and optional CIP setups to help you maintain compliance without the mess.
Bonus Feature: Scalability That Grows with You 🚀
As your business grows, your equipment should too. Scalability is a key consideration in modern manufacturing, and Apex systems are designed to adapt:
-
Start with semi-automatic machines
-
Upgrade to multi-head, fully automated lines
-
Add components like cappers, labelers, conveyors, and more
FAQs
1. Can one filling system handle multiple products?
Yes! Apex’s modular systems are designed for quick changeovers and adjustable controls, allowing you to run different product types on the same line.
2. What’s the best filling system for high-viscosity products?
Piston fillers are ideal for thick products like sauces, creams, and gels. For precision and flow control, we also offer servo-driven solutions.
3. How much training does a new operator need?
Minimal! Our user-friendly systems come with onsite or virtual training and intuitive control panels that reduce onboarding time.
4. How can I reduce downtime during cleaning or maintenance?
Choose a system with tool-less parts, CIP compatibility, and easy-access components—all standard features in Apex equipment.
Partner with Apex to Find the Right System for You
At Apex Filling Systems, we know your success depends on more than just machinery. It requires a trusted partner, built-in scalability, and a deep understanding of your industry. Whether you’re filling beverages, beauty products, chemicals, or nutritional supplements, our systems are built to deliver:
✅ Precision
✅ Efficiency
✅ Flexibility
✅ Ease of use
✅ Compliance
Ready to level up your liquid filling operations?
👉 Contact Apex Filling Systems today for a consultation.
👉 Explore our full range of customizable liquid filling machines.
Share this
- Help First (78)
- Filling Equipment (32)
- Informational (29)
- Apex Filling Systems (25)
- Industry Insights (25)
- Automatic Filling Machine (23)
- About Apex (19)
- Packaging Equipment (18)
- Apex Filling (10)
- Automatic Capping (10)
- Fillers (10)
- Apex (7)
- Uncategorized (5)
- American Made Goods (3)
- Apex Family (2)
- Absolute Truth (1)
- Apex Team (1)
- Apex Way (1)
- Petroleum (1)
- oil (1)
- April 2025 (5)
- March 2025 (10)
- February 2025 (12)
- January 2025 (14)
- December 2024 (1)
- November 2024 (4)
- October 2024 (4)
- September 2024 (2)
- August 2024 (1)
- July 2024 (4)
- October 2022 (1)
- September 2022 (1)
- June 2022 (1)
- October 2021 (2)
- June 2021 (1)
- May 2021 (1)
- April 2021 (2)
- March 2021 (2)
- February 2021 (1)
- January 2021 (2)
- November 2020 (1)
- October 2020 (1)
- September 2020 (2)
- August 2020 (1)
- July 2020 (1)
- June 2020 (1)
- May 2020 (1)
- April 2020 (2)
- March 2020 (2)
- February 2020 (2)
- January 2020 (3)
- December 2019 (2)
- November 2019 (6)
- October 2019 (4)
- September 2019 (3)
- August 2019 (6)
- July 2019 (2)
- April 2019 (1)
- February 2019 (1)
- January 2019 (7)
- December 2018 (6)
- November 2018 (5)
- October 2018 (2)
- September 2018 (2)
- August 2018 (1)
- July 2018 (3)
- May 2018 (2)
- April 2018 (1)
- March 2018 (2)
- February 2018 (2)
- January 2018 (2)