Share this
Maximizing Speed and Accuracy in a Bottling Machine
by APEX Filling Systems on Mar 24, 2025
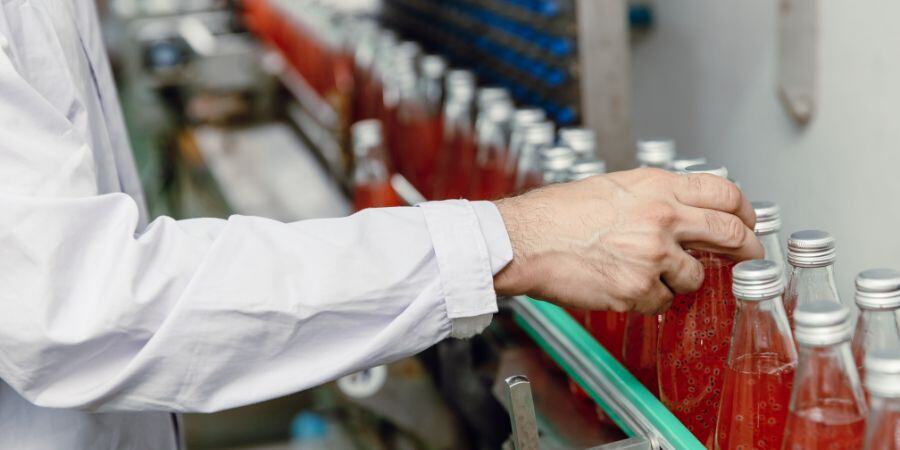
Achieving the perfect balance between speed and accuracy is essential in bottling operations. Whether you’re bottling beverages, cosmetics, or pharmaceuticals, your bottling machine's performance directly impacts production efficiency and product quality.
To stay competitive, manufacturers must adopt strategies that enhance efficiency, maintain consistency, and minimize errors. In this blog, Apex Filling Systems explores five actionable strategies for maximizing the performance of your bottling machine.
1. Upgrade to High-Performance Bottling Machines
The foundation of a successful bottling operation lies in the equipment. High-performance bottling machines are designed to enhance efficiency and precision, giving manufacturers an edge in competitive markets. Here are some key features to consider:
- Servo-Controlled Systems: Ensure precise fill levels and cap torque with advanced control technology. These systems are crucial for maintaining accuracy, especially when dealing with products that require tight tolerances.
- Multi-Head Fillers: Increase throughput by filling multiple containers simultaneously. This feature allows manufacturers to meet high production demands without compromising on quality.
- Customizable Settings: Easily accommodate different bottle sizes and product viscosities. Customization reduces downtime caused by changeovers and increases flexibility in production.
2. Optimize Conveyor and Indexing Systems
Efficient conveyance is critical for seamless bottling operations. Bottles must transition smoothly between stages to avoid delays, spillage, or errors. Optimization strategies include:
- Indexing Conveyors: Precisely positioning bottles for filling and capping ensures accurate alignment and minimizes the risk of spillage or misplacement.
- Variable-Speed Controls: Adjust conveyor speeds to match production rates and prevent bottlenecks. This flexibility ensures a steady workflow, regardless of fluctuations in production demand.
- Durable Materials: Use high-quality materials for conveyors to reduce wear and tear. Robust conveyors minimize maintenance needs and extend equipment lifespan.
3. Maintain a Strict Quality Control Process
Quality control is essential for protecting your brand’s reputation and ensuring customer satisfaction. Incorporating advanced quality control measures can drastically reduce errors and wastage:
- Vision Inspection Systems: Detect fill level inaccuracies, misaligned caps, or label defects. These systems catch issues in real-time, ensuring only perfect bottles proceed through the line.
- Dynamic Weight Checkers: Ensure each bottle meets weight standards, preventing inconsistencies that could lead to customer complaints or regulatory issues.
- Automated Reject Mechanisms: Remove defective bottles from the line to maintain overall quality. Automation ensures faulty products don’t reach the end consumer, safeguarding your brand.
4. Implement Preventive Maintenance Plans
Even the best bottling machines require maintenance to operate at peak performance. A proactive maintenance plan minimizes downtime and extends the life of your equipment:
- Scheduled Cleaning: Keep components free of residue to prevent contamination and ensure product safety. Regular cleaning also keeps equipment running efficiently.
- Lubrication Schedules: Reduce friction and wear with regular lubrication. Proper lubrication minimizes mechanical failures and keeps machines running smoothly.
- Diagnostic Tools: Advanced tools monitor equipment health and predict maintenance needs. Diagnostics can identify potential issues before they escalate, reducing costly downtime.
5. Train Staff on Equipment Best Practices
Your bottling machine is only as effective as the team operating it. Well-trained staff ensure optimal performance, fewer errors, and improved safety:
- Calibration Techniques: Train operators to adjust settings for optimal performance. Proper calibration ensures consistent fills and minimizes material waste.
- Troubleshooting Common Issues: Equip employees with the skills to resolve minor malfunctions quickly. This reduces reliance on technicians and minimizes downtime.
- Safety Standards: Ensure adherence to safety protocols to protect workers and maintain compliance. A focus on safety also improves overall productivity.
Achieving Excellence in Bottling Operations With Continuous Improvement
Your bottling machine can deliver unmatched efficiency and consistent results by optimizing speed and accuracy.
Adopting a continuous improvement mindset is essential as market demands and technologies evolve. Regularly evaluating your bottling processes, investing in equipment upgrades, and prioritizing staff training can keep your operations efficient and competitive. With consistent focus and the right strategies, your bottling operations can drive business growth and success.
Share this
- Help First (78)
- Filling Equipment (30)
- Informational (29)
- Industry Insights (25)
- Apex Filling Systems (23)
- Automatic Filling Machine (22)
- About Apex (19)
- Packaging Equipment (16)
- Apex Filling (9)
- Automatic Capping (9)
- Fillers (9)
- Apex (7)
- Uncategorized (5)
- American Made Goods (2)
- Absolute Truth (1)
- Apex Family (1)
- Apex Way (1)
- Petroleum (1)
- oil (1)
- April 2025 (1)
- March 2025 (10)
- February 2025 (12)
- January 2025 (14)
- December 2024 (1)
- November 2024 (4)
- October 2024 (4)
- September 2024 (2)
- August 2024 (1)
- July 2024 (4)
- October 2022 (1)
- September 2022 (1)
- June 2022 (1)
- October 2021 (2)
- June 2021 (1)
- May 2021 (1)
- April 2021 (2)
- March 2021 (2)
- February 2021 (1)
- January 2021 (2)
- November 2020 (1)
- October 2020 (1)
- September 2020 (2)
- August 2020 (1)
- July 2020 (1)
- June 2020 (1)
- May 2020 (1)
- April 2020 (2)
- March 2020 (2)
- February 2020 (2)
- January 2020 (3)
- December 2019 (2)
- November 2019 (6)
- October 2019 (4)
- September 2019 (3)
- August 2019 (6)
- July 2019 (2)
- April 2019 (1)
- February 2019 (1)
- January 2019 (7)
- December 2018 (6)
- November 2018 (5)
- October 2018 (2)
- September 2018 (2)
- August 2018 (1)
- July 2018 (3)
- May 2018 (2)
- April 2018 (1)
- March 2018 (2)
- February 2018 (2)
- January 2018 (2)