Share this
5 Factors for Choosing the Right Filling Equipment for Your Business
by APEX Filling Systems on Oct 21, 2024
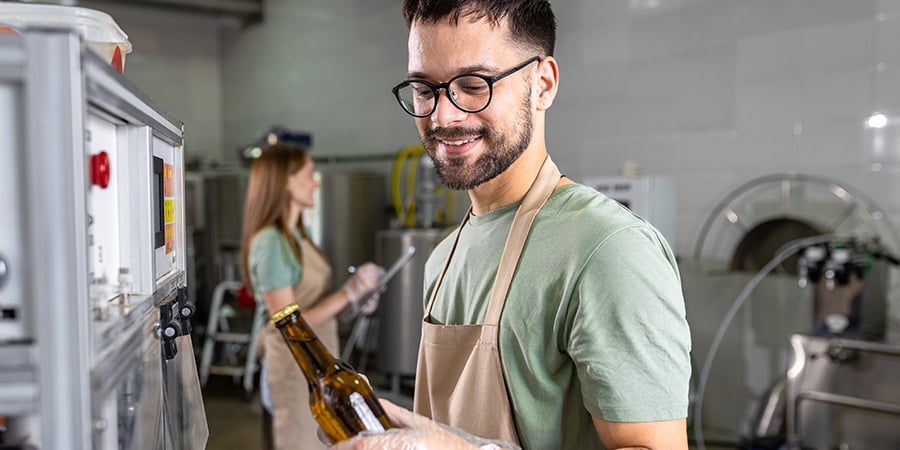
Choosing the right filling equipment is critical for efficient business production. Oftentimes, when businesses face challenges, it is because of a lack of clarity on key factors like material compatibility, production volume, speed and accuracy requirements, scalability, and budget constraints.
It can be challenging to evaluate all of these factors simultaneously. Without a structured approach, businesses risk investing in equipment that may not meet their needs, leading to inefficiencies, production bottlenecks, and increased costs. In this blog, we will review five key factors for determining if an industrial filling machine is right for you, including method of filling, levels of automation, container shape, compatibility with other systems, and reliability and ease of use.
Methods of Filling for Best Product Packaging
There are many different methods used for liquid filling machines. The type of filling process you should use is based on the type of product you are using and the intended visual appeal after filling. Some of the main filling methods include overflow, piston, gravity, and pump fillers.
Overflow Fillers for Even Fill Levels
Overflow fillers are great for products where businesses want to create the appearance of even fill levels, regardless of container irregularities and varying product volumes. These types of fillers are often used for retail products that get arranged side-by-side on a shelf. Because this causes the products to look more uniform, it reduces the likelihood of buyers rejecting one item over another because of the perception of less product. This filling type is quick for filling products. It works best with thin to medium-viscosity products.
Piston Fillers for Reduced Waste
Piston fillers are the perfect liquid filling machine solution for thin to thick viscosity products, as well as semi-solids and liquids with particulates. These filling machines are designed to dispense products in precise amounts and create minimal waste. Piston fillers are often used for pharmaceutical use or expensive products where having precise amounts is extra important.
Gravity Fillers for Cost-Effective Low Viscosity Filling
Gravity fillers are great liquid filling machine options for free-flowing, low-viscosity, or frothy liquids that do not contain particles. This method involves allowing the liquid's natural flow to take it down into the containers. All product is stored above in a storage tank above their containers, allowing gravity to do the work using time-based filling to ensure equal filling levels. This is typically the most cost-effective filling method.
Pump Fillers for Easier Change Overs
Pump fillers are a very versatile liquid filling solution that can process substances of any viscosity. They are often used for products that are harder to work with, such as thick, chunky, stretchy, or drippy products. These liquid filling machines allow for easy changeovers and are ideal for those who need to make regular changes between different containers. Pump fillers can be great options for filling containers with products such as cosmetic creams, heavy sauces, honey, gels, shampoos, conditioners, paste cleaners, and car wax.
Levels of Automation and Improved Production
Different machines include different levels of automation. Automation decreases the likelihood of human error and improves factors such as speed, accuracy, and consistency in filling products. The three different levels of automation include manual, semi-automatic, and fully automatic filling machines.
Manual Filling Machines for Small Businesses
As the name suggests, manual filling machines require human operators instead of electricity to run. These types of machines may work for very small businesses that are just starting out and produce about 15 containers a minute. As demand increases, however, manual filling can quickly be removed as an option.
Semi-Automatic Filling Machines for Double the Output
Semi-automatic liquid filling machines more than double the output of manual machines. These machines require a little more setup but assist the operators with their filling work, helping increase speed and efficiency.
Automatic Filling Machines for High-Level Production Efficiency
Finally, there are fully automatic industrial filling machines. These machines require no human assistance and run on electricity and user-friendly interfaces. These are perfect for larger businesses that require larger outputs and can fill about 100 containers per minute. The vast majority of the work is done by machine alone, including organization sealing, filling, labeling, and moving products through the system. This creates the highest level of speed and production efficiency
The type of machine you need depends on various factors, including production volume, complexity, and budget considerations. The less manual work involved, the more expensive and complex the setup becomes. However, those machines are the most efficient and require less work once they are set up. More manual machines are cheaper but require more work and produce smaller outputs.
Different Machines for Different Container Shapes
The type of liquid isn’t the only consideration you need when it comes to your product. The container being filled also has an impact on what machine should be used. For example, if you are trying to fill a bottle with a more narrow opening, you may need a machine that can accommodate precise nozzles to fill in those openings.
The shape and size of containers also directly affect filling speed and accuracy. Containers with wider openings generally allow for faster filling because they provide easier access for filling nozzles. If using the wrong machine doesn’t allow enough product to flow through, it can also slow down the process and require longer cleaning times.
If you are trying to fill multiple types of product containers, a more versatile machine with easier changeovers, like a pump filler, may be your best option. You will also have to consider whether it is more of a priority for even fill levels or even-looking filling levels, as that can also impact the type of machine you should use.
Compatibility with Existing Product Systems
Especially if this isn’t your first machine, it is also important to make sure whatever new machine you are buying is compatible with your existing systems, such as those for labeling, packing, and quality control. Having too many complex systems can lead to overly complicated workflows and increases the likelihood of incompatible protocols.
Compatible machines, on the other hand, can be easily integrated into your current production line, minimizing disruptions and downtime during installation and setup. Compatibility is also necessary for making sure there is consistent product quality and filling accuracy across your production line so that you can continue to meet customer expectations and regulatory requirements
One way to make sure equipment works with your production line is by having an IFAT (Internal Factory Acceptance Test). These tests are used to evaluate liquid filling equipment during and after the assembly process and make sure it is operating the way it was planned to.
Reliability and Ease of Use for Maximum Efficiency
It is important to choose a reliable liquid filling machine for your products. The more reliable the machine, the less chance there is of unexpected downtown. It also helps increase productivity. When choosing a brand to buy from, make sure they have your best intentions in mind.
You’ll want to look for features in your machine that are user-friendly and ergonomic options for more comfortable use and operational efficiency for your team. You will also want to find a brand that has turnkey products that will easily integrate with one another for filling, capping, conveying, labeling, and more.
Not every machine and industry is the same. There is no “one-size-fits-all.” During the selection process, make sure to speak with specialists or representatives to help come up with a detailed plan and make sure all equipment fits in with your industry standards. They should be able to help guide you toward which machine will be easiest to use and be the most reliable for filling your specific product type, as well as help you determine which machines fit your industry's standards.
Deciding Which Filling Machine is Right For You
Choosing the right filling equipment requires taking a systematic approach. Before making a final decision, make sure of key factors like method of filling, levels of automation, container shape, compatibility with other systems, reliability, and ease of use. By assessing material compatibility, analyzing production volumes, evaluating speed and accuracy capabilities, selecting scalable equipment, and determining which is the best solution within their budget, businesses can make informed decisions, mitigate risks, and optimize their filling operations for efficiency and competitiveness.
Share this
- Help First (78)
- Filling Equipment (32)
- Informational (29)
- Apex Filling Systems (25)
- Industry Insights (25)
- Automatic Filling Machine (23)
- About Apex (19)
- Packaging Equipment (18)
- Apex Filling (10)
- Automatic Capping (10)
- Fillers (10)
- Apex (7)
- Uncategorized (5)
- American Made Goods (3)
- Apex Family (2)
- Absolute Truth (1)
- Apex Team (1)
- Apex Way (1)
- Petroleum (1)
- oil (1)
- April 2025 (5)
- March 2025 (10)
- February 2025 (12)
- January 2025 (14)
- December 2024 (1)
- November 2024 (4)
- October 2024 (4)
- September 2024 (2)
- August 2024 (1)
- July 2024 (4)
- October 2022 (1)
- September 2022 (1)
- June 2022 (1)
- October 2021 (2)
- June 2021 (1)
- May 2021 (1)
- April 2021 (2)
- March 2021 (2)
- February 2021 (1)
- January 2021 (2)
- November 2020 (1)
- October 2020 (1)
- September 2020 (2)
- August 2020 (1)
- July 2020 (1)
- June 2020 (1)
- May 2020 (1)
- April 2020 (2)
- March 2020 (2)
- February 2020 (2)
- January 2020 (3)
- December 2019 (2)
- November 2019 (6)
- October 2019 (4)
- September 2019 (3)
- August 2019 (6)
- July 2019 (2)
- April 2019 (1)
- February 2019 (1)
- January 2019 (7)
- December 2018 (6)
- November 2018 (5)
- October 2018 (2)
- September 2018 (2)
- August 2018 (1)
- July 2018 (3)
- May 2018 (2)
- April 2018 (1)
- March 2018 (2)
- February 2018 (2)
- January 2018 (2)