Share this
The Apex Guide to Automatic Gravity Fillers
by APEX Filling Systems on Jul 01, 2024
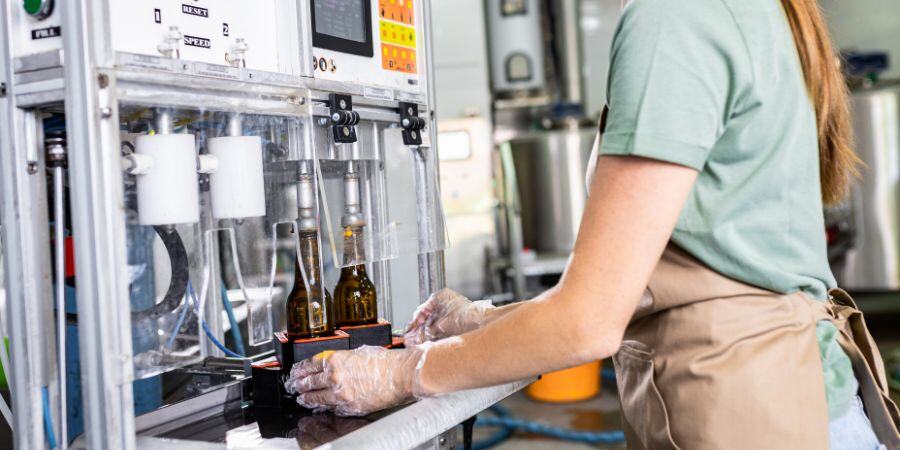
Liquid-filling machines are designed to be capable of filling a variety of containers with a variety of different liquid types. These include free-flowing liquids, viscous or thick liquids, foamy products, products that string or drip, and products with particulates or chunks. The purpose of these machines is to streamline the liquid-filling process. Gravity-filling machines are the simplest filling method. They are designed to offer precise volumetric time-based filling for products ranging from thin to medium viscosity. It is a highly efficient and easily automatable solution.
Efficient and accurate filling processes are crucial. They maximize productivity, maintain product quality, and reduce costs. These processes minimize downtime and ensure each container holds the correct amount, preventing wastage and ensuring consistency. They also reduce material costs, improve profit margins, and ensure regulatory compliance and smooth operations. Efficient and accurate filling processes are necessary for the success and profitability of any production line.
As companies grow, they often face the decision of whether to continue hand-filling containers or invest in automated filling equipment to enhance their production systems. Although there are many options, gravity fillers offer distinct advantages that address common issues faced by operators and technicians. Gravity fillers significantly improve speed and efficiency. This allows businesses to increase production and capture larger market shares. These machines also make sure all bottle-filling is precise and consistent. This reduces product waste and mess. Additionally, automated systems enhance worker safety by minimizing manual labor and potential injuries. They also have higher hygienic standards by reducing human contact with products. By consulting with manufacturers who prioritize long-term customer success and adaptability, companies can effectively transition to automation, ensuring durable and reliable machinery that meets their needs as they grow.
Understanding How Gravity Fillers Work
A gravity filler has a hopper placed up above a set of nozzles, which is then filled with the liquid to be bottled. Once the bottles are placed below the nozzles, the nozzle valves can open, and gravity works to draw the product down. The valve is timed to shut again after a precise amount of product has flowed into the containers, and then new containers can be set underneath the valves so the process can begin again.
The Best Liquids for Gravity Filling Machines
Our Economy Automatic Gravity Filler and our Pro Model Gravity Filler machines work best with low to medium viscosity or frothy liquids, such as water rather than mayonnaise. The product also should be free of any chunks or particles that could clog the nozzle, and it should have a uniform consistency throughout. The fill is volumetric based on time, with thicker liquids requiring a slightly longer fill time than the same volume of low viscosity liquids. The same volume of product will be dispensed each time.
These machins can be found in industries that include food and beverage, specialty chemical and cosmetics and personal care, provided the product is free-flowing and has a low viscosity. Most recently, many manufacturers have been using the gravity-filling process to meet the high demand for hand sanitizer. Because hand sanitizer is flammable, the filler has to be customized with explosion-proof controls, and you can turn to our experts to guide you through the process.
Given the right set of conditions, gravity filling can be a good choice for a company looking for an economical and simple automatic process.
Techniques for Handling Different Types of Liquids and Viscosity Variations
Different liquids have different viscosity — or thicknesses. This factor is one of the most important factors to consider before investing in-line filling systems of any scale. For example, a thick liquid will require a different set of nozzles than those used for more runny liquids. Another factor to consider in relation to viscosity is the matter of the product you are dealing with—such as if it is just a smooth fluid or if there are particulates in it, such as facial cleanser beads or food particles.
Depending on the liquid’s viscosity, you may need one of two types of machines—a piston filler, which is used for liquids of higher viscosity, or non-piston machines that rely on just gravity, which is better suited for more liquid products. While these machines don’t require pistons to push liquids through with more force, they will need leak-proof valves to ensure the correct volume of liquid is dispensed each time. The use of the correct machinery will help you maintain consistency across various liquid types.
Increased Level of Automation for the Production Line
Finding the right level of automation depends on knowing which balance of speed and cost is best for your company. Unlike manual filling machines, which are used by a single operator to fill one container at a time, or semi-automatic filling machines that still require some manual operation, automatic filling machines like automatic gravity fillers are the best choice for large-scale companies with high production requirements. They take up the most space, are usually connected to conveyance systems, and require the least manual operation.
When working out which system best fits your budget, factor in the level of growth you are expecting over the next few years so the equipment you purchase today will continue to meet your production demands over time. The number of containers you can fill per hour depends on the viscosity of your product, the volume of your containers, and the number of fill heads used. When you have taken these variables into account, you can better project the cost savings of automation based on your own specific situation.
Optimizing Fill Levels for Accuracy and Efficiency
Optimizing fill levels is important to ensure the machine works at maximum efficacy and there are no unnecessary losses or spills. Luckily, gravity automatic liquid filling machines have many features that make them very easy to work with. For example, there are sensors such as a “no bottle/no fill” sensor to prevent loss and spills and a bottle backup sensor that delays filler operation until any jam is cleared. Additionally, there is a user-friendly touchscreen HMI (human-machine interface) that can be used to easily adjust both the speed of filling and the volume of the filling.
Gravity fillers also use a time-based filling principle. Pre-set nozzle opening time and more accurate interior volume can be achieved this way. Keeping equipment calibrated, maintaining product consistency, and making the best use of these high-tech sensors make sure that measurements are accurate. Setting up routine quality checks and running machines at the right speed help things run smoothly. By combining these methods, the filling process can remain simple without compromising accuracy.
Built-in Technology and Ease of Use
Economy Automatic Gravity Filler and our Pro Model Gravity Filler are proudly manufactured in the United States. Our state-of-the-art machines are easy to use and are designed to accommodate future upgrades. Every purchase is backed by our guarantee of quality and commitment to service. Some of the standout features of our gravity fillers include an Allen Bradley PLC (programmable logic controller) that brings the power of "smart" computers to a rugged industrial environment, a user-friendly touch screen HMI (human-machine interface) for easy speed and volume adjustments, and the option of one to 16 fill heads.
Economy Automatic Gravity Filler
The Economy Automatic Gravity Filler offers a seamless entry into gravity filling, ready for swift delivery. Designed for thin to medium viscosity products, this machine utilizes a volumetric time-based fill method, ensuring precise and consistent fill volumes. Perfect for thin liquids with a uniform viscosity, this gravity filler is easily automated for efficiency and accuracy.
Key Benefits | Options |
|
|
See all details for Economy Gravity Filler
Pro Model Gravity Filler
The Pro Model Gravity Filler is designed to deliver precise and consistent volumetric time-based filling for thin to medium viscosity products. Its innovative gravity filling method ensures repeatable and accurate fill volumes every time, making it the perfect choice for thin liquids with a uniform viscosity profile.
Key Benefits | Options |
|
|
See all details for Pro Model Gravity Filler
Customization Options
In addition to our standard features, our fillers are designed to be compatible with conveyance systems, capping solutions, and labelers. Our Economy Automatic Gravity Filler and our Pro Model Gravity Filler enhance your production capabilities with many available customization options for filling mechanisms, including automatic drip trays for cleanliness and precision, bottom-up filling to minimize foaming, and positive shut-off nozzles for drip-free performance. There are also available features for simplified handling and compatibility, like bottle grabbers, neck grabbers, and flexible indexing options such as star wheel or timing screw mechanisms.
- Automatic drip tray
- Bottle grabbers and neck grabbers
- Star wheel or timing screw indexing
- Clean-in-place system
- Hazardous location/environment construction – Class I, Division II, Group
- C&D
- All-pneumatic construction
- Corrosion resistant construction, including all contact parts
- Product agitation and mixing
- Diving heads
- Bottom up filling
- Sanitary style construction
- High temperature applications
- Positive shut off nozzles
- Various fill head and nozzle sizes
Proper Setup, Calibration, and Maintenance Procedures
No matter what you use your gravity filler for, it is important to ensure proper setup, calibration, and maintenance procedures are followed.
Importance of Correct Setup for Optimal Performance
Gravity bottle filler machines include components such as frames, filler bowls, product supply tanks, filling valves, product pathways, and nozzles. Correct setup is essential for liquid fillers to operate at maximum efficiency. This includes properly installing and aligning all components according to manufacturer guidelines. Misalignment can cause issues like inconsistent fill levels, leakage, and premature wear on parts. Ensuring the right settings for liquid viscosity, fill volumes, and machine speed is also critical for accurate and consistent filling.
Calibration Techniques for Precision Filling
Regular calibration is necessary to maintain precise fill levels over time, as components can shift slightly due to wear. Common calibration methods include using certified test weights, substituting weighed material like water or sand, or comparing the output to a calibrated secondary scale. Make sure your team is up-to-date on how to follow these procedures. Calibrating at the target fill weight range provides the highest accuracy for that product.
Maintenance Procedures to Ensure Longevity and Consistency
Preventive maintenance is key to maximizing a liquid filler's lifespan and performance. Luckily, gravity bottle filling machines require little maintenance due to their simple design. However, some routine maintenance may be done to keep the machine working smoothly and running for a long. This includes regular cleaning of filler bowls, product supply tanks, valves, and nozzles and periodically checking the filling valves and seals for wear and tear and replacing them as necessary.
Other maintenance procedures may include checking the frame and supports, monitoring product pathways, keeping moving parts lubricated, and calibrating filling mechanisms. By properly setting up, calibrating, and maintaining liquid filling equipment according to best practices, manufacturers can optimize accuracy, minimize downtime, and extend the usable life of their investment.
Ensuring Product Quality and Regulatory Compliance
Although gravity-automatic liquid filling machines are heavily automated, it is important to maintain quality control measures in the filling process. There are different regulatory standards and compliance requirements based on the products you are dealing with. For example, liquid filling machines used in the food industry must follow the FDA’s health and consumer protection guidelines. This means keeping in mind factors such as keeping paths clean, non-corrosive, sealed, and preventing moisture from entering.
Other industries may have different sets of guidelines to follow, such as those dealing with more toxic or flammable materials. Remember, these types of machines are best suited for liquids of thinner viscosities such as water, solvents, alcohol, specialty chemicals, paint, inks, and corrosive chemicals like acids and bleach. It is always best to keep up-to-date on the latest standards and compliance requirements to make adjustments as needed.
Taking the Next Steps Towards Greater Efficiency
Gravity automatic liquid fillers provide a versatile and efficient solution for filling a variety of containers with liquids ranging from free-flowing to medium viscosity. These liquid filling machines streamline the filling process with features such as “no bottle/no fill” sensors, user-friendly touchscreens, and precise time-based filling mechanisms. Compared to their semi-automatic filling machine alternatives, automatic filling machines have simplified upkeep and use.
These machine’s lifespans can be further extended by proper setup, guidance, calibration, and maintenance. This is also essential for optimizing performance and ensuring accurate fill levels. Operators and technicians can enhance efficiency and accuracy by implementing regular calibration, maintaining product consistency, and using advanced sensors. As companies grow, transitioning to automated filling systems like gravity bottle fillers can significantly boost productivity, reduce waste, and improve worker safety. These bottle-filling machines can be customized to meet specific industry needs, from substances of low to medium viscosity to frothy liquids.
If you're seeking to enhance the efficiency of your production and packaging lines, don't hesitate to reach out. Our team of specialists is well-equipped to grasp the specific needs of your setups and provide tailored solutions to optimize your filling processes.
Alicia Cannon

Integrity, honesty, and a dedication to delivering ambitious results serve as the central themes of Alicia’s career and are evident in every interaction she has with our clients. Her relationship-centered leadership style has paved the way for Apex Filling System’s culture of compassion & empathy, executed with accountability that ensures consistently great outcomes. As a learner for life, her pursuit of continuous personal and professional growth has led Apex Filling Systems to be recognized as an industry innovator in customer experience. Holding advanced degrees in the areas of engineering and management, she has a unique ability to analyze processes, identify potential problems before they arise, and develop standardized solutions to ensure every client of Apex Filling Systems enjoys a hassle-free, professional, and pleasant experience. Her leadership style has been influenced by the work of some of the most well-regarded thought leaders throughout the last 50 years. Among them are Jim Collins, Sally Hogshead, John Maxwell, and Tony Robbins.
Share this
- Help First (78)
- Filling Equipment (30)
- Informational (29)
- Industry Insights (25)
- Apex Filling Systems (24)
- Automatic Filling Machine (22)
- About Apex (19)
- Packaging Equipment (17)
- Apex Filling (10)
- Automatic Capping (10)
- Fillers (9)
- Apex (7)
- Uncategorized (5)
- American Made Goods (3)
- Absolute Truth (1)
- Apex Family (1)
- Apex Way (1)
- Petroleum (1)
- oil (1)
- April 2025 (3)
- March 2025 (10)
- February 2025 (12)
- January 2025 (14)
- December 2024 (1)
- November 2024 (4)
- October 2024 (4)
- September 2024 (2)
- August 2024 (1)
- July 2024 (4)
- October 2022 (1)
- September 2022 (1)
- June 2022 (1)
- October 2021 (2)
- June 2021 (1)
- May 2021 (1)
- April 2021 (2)
- March 2021 (2)
- February 2021 (1)
- January 2021 (2)
- November 2020 (1)
- October 2020 (1)
- September 2020 (2)
- August 2020 (1)
- July 2020 (1)
- June 2020 (1)
- May 2020 (1)
- April 2020 (2)
- March 2020 (2)
- February 2020 (2)
- January 2020 (3)
- December 2019 (2)
- November 2019 (6)
- October 2019 (4)
- September 2019 (3)
- August 2019 (6)
- July 2019 (2)
- April 2019 (1)
- February 2019 (1)
- January 2019 (7)
- December 2018 (6)
- November 2018 (5)
- October 2018 (2)
- September 2018 (2)
- August 2018 (1)
- July 2018 (3)
- May 2018 (2)
- April 2018 (1)
- March 2018 (2)
- February 2018 (2)
- January 2018 (2)