Share this
The Latest Innovations in Filling Equipment Technology
by APEX Filling Systems on Feb 10, 2025
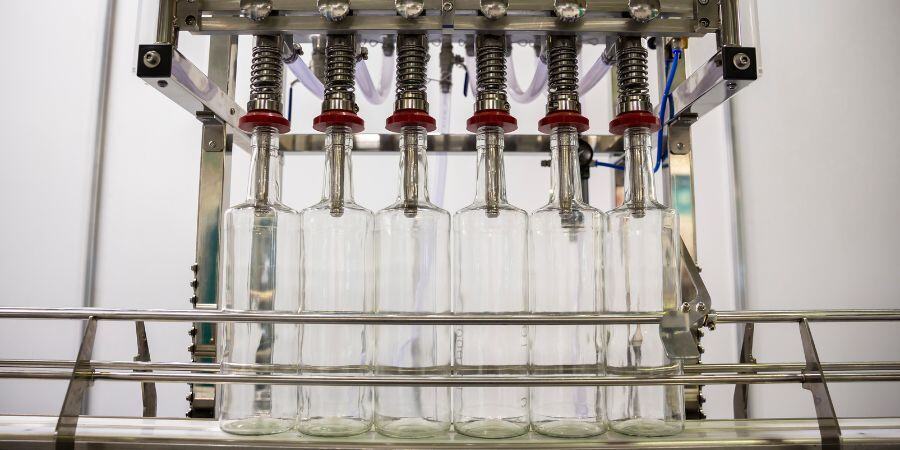
The ever-evolving packaging industry continues to leverage cutting-edge technologies to enhance efficiency, precision, and sustainability. At the center of this transformation is Apex Filling Systems bottle filling and capping machines, a key player in ensuring seamless production across industries such as food and beverage, pharmaceuticals, and cosmetics. With advancements ranging from intelligent automation to eco-friendly designs, these machines are setting new benchmarks for performance and reliability.
Technological improvements empower manufacturers to overcome production bottlenecks, reduce waste, and improve quality control. Apex explores the latest bottle-filling and capping machine innovations and highlights their benefits to modern production lines.
1. AI-powered Smart Filling Systems
Artificial intelligence is revolutionizing filling equipment by introducing intelligent, self-learning systems. Machines now feature predictive maintenance tools that monitor wear and tear, alerting operators to potential issues before they escalate. Adaptive filling technology adjusts parameters like fill levels and speeds to accommodate changes in product viscosity or bottle sizes.
Innovative systems analyze operational data to optimize performance, including identifying patterns in downtime or errors, enabling operators to implement targeted improvements. Additionally, AI can enhance resource allocation by predicting production volumes and adjusting machine operations accordingly. These AI-driven capabilities significantly reduce downtime, minimize waste, and ensure consistent product quality, making them indispensable for high-volume production lines.
AI integrates into filling equipment and supports multi-product lines. Machines with learning algorithms can quickly adapt to different products, reducing changeover times and increasing overall line efficiency. This adaptability is a game-changer for industries requiring frequent production shifts.
Moreover, AI can be utilized to ensure compliance with industry standards. By analyzing and recording production data, it assists in generating reports that simplify audits and inspections.
2. Precision with Advanced Measurement Systems
Precision is critical in filling machine operations, especially in pharmaceutical industries that require exact measurements. Apex Filling Systems' modern equipment incorporates advanced technologies, including mass flow meters, ensuring precise fill levels even for high-viscosity liquids. Multi-head fillers further improve efficiency by handling multiple containers simultaneously while maintaining accuracy.
Advanced measurement systems also support greater flexibility in product lines. Apex Filling Systems machines handle a range of container sizes and shapes without requiring extensive manual adjustments. Enhanced precision reduces the risk of costly recalls and helps maintain brand trust. As product regulations become increasingly stringent, investing in machines equipped with state-of-the-art measurement systems ensures compliance and consumer confidence.
Apex’s precision technologies also reduce material waste, improving sustainability by using only what is needed for each fill. This reduces costs associated with overfills and defective packaging, making precision an essential feature in modern filling equipment.
3. Energy-efficient and Eco-Friendly Designs
Manufacturers have prioritized sustainability, and Apex Filling Systems equipment is evolving to meet these demands. Energy-efficient motors and pumps reduce power consumption, while optimized material use minimizes packaging waste. Additionally, machines designed to handle biodegradable or recycled materials are becoming more common, helping businesses align with eco-conscious consumer preferences.
Manufacturers are also adopting solar-powered components and advanced insulation technologies to lower their carbon footprint further. New machine designs aim to balance environmental impact with operational performance. These features lower operating costs and enhance the ecological profile of manufacturing processes, making sustainability a competitive advantage.
Incorporating water-saving technologies in the cleaning processes of these machines is another notable advancement. Manufacturers can save resources by reducing water usage during maintenance and operations while maintaining optimal hygiene standards.
4. Enhanced Cleaning and Sterilization Features
Maintaining hygiene is crucial, particularly in industries like food and pharmaceuticals. Innovations such as Clean-in-Place systems automate cleaning processes, eliminating the need for disassembly. UV light sterilization is also gaining traction, providing effective bacteria control without harsh chemicals.
Moreover, improved cleaning protocols reduce the risk of cross-contamination during product changeovers. These advancements simplify compliance with health and safety standards while reducing downtime associated with manual cleaning. Automated systems also save labor costs and improve cleaning consistency across shifts.
Hygiene-focused innovations extend to machine materials as well. Non-porous and corrosion-resistant materials are now standard in equipment design, ensuring longer lifespans and easier maintenance.
5. Seamless IoT Integration
The Internet of Things (IoT) connects filling machines to broader production systems, creating more intelligent and efficient workflows. Remote monitoring capabilities allow operators to track performance and address issues in real time, while cloud-based analytics offer insights into optimizing operations.
IoT-enabled machines ensure synchronized operations across production lines, reducing bottlenecks and enhancing overall efficiency. Advanced data sharing between systems fosters better inventory management and on-demand production adjustments. This level of connectivity allows manufacturers to respond quickly to changing market demands.
Beyond operational benefits, IoT integration improves equipment diagnostics. Technicians can remotely identify and resolve issues, reducing downtime and repair costs,
Transform Your Packaging Landscape with Apex Filling Systems
Advancements in Apex Filling Systems bottle filling and capping machines are revolutionizing production lines, enabling manufacturers to achieve new efficiency, precision, and sustainability levels. These innovations address industry challenges and create opportunities for growth in an increasingly competitive market.
Explore how Apex Filling Systems' innovative technologies transform the entire automated packaging system, from filling to labeling.
Share this
- Help First (78)
- Filling Equipment (32)
- Informational (29)
- Apex Filling Systems (25)
- Industry Insights (25)
- Automatic Filling Machine (23)
- About Apex (19)
- Packaging Equipment (18)
- Apex Filling (10)
- Automatic Capping (10)
- Fillers (10)
- Apex (7)
- Uncategorized (5)
- American Made Goods (3)
- Apex Family (2)
- Absolute Truth (1)
- Apex Team (1)
- Apex Way (1)
- Petroleum (1)
- oil (1)
- April 2025 (5)
- March 2025 (10)
- February 2025 (12)
- January 2025 (14)
- December 2024 (1)
- November 2024 (4)
- October 2024 (4)
- September 2024 (2)
- August 2024 (1)
- July 2024 (4)
- October 2022 (1)
- September 2022 (1)
- June 2022 (1)
- October 2021 (2)
- June 2021 (1)
- May 2021 (1)
- April 2021 (2)
- March 2021 (2)
- February 2021 (1)
- January 2021 (2)
- November 2020 (1)
- October 2020 (1)
- September 2020 (2)
- August 2020 (1)
- July 2020 (1)
- June 2020 (1)
- May 2020 (1)
- April 2020 (2)
- March 2020 (2)
- February 2020 (2)
- January 2020 (3)
- December 2019 (2)
- November 2019 (6)
- October 2019 (4)
- September 2019 (3)
- August 2019 (6)
- July 2019 (2)
- April 2019 (1)
- February 2019 (1)
- January 2019 (7)
- December 2018 (6)
- November 2018 (5)
- October 2018 (2)
- September 2018 (2)
- August 2018 (1)
- July 2018 (3)
- May 2018 (2)
- April 2018 (1)
- March 2018 (2)
- February 2018 (2)
- January 2018 (2)