Share this
Understanding Different Types of Liquid Filling Machines: An In-Depth Guide
by APEX Filling Systems on Jul 29, 2024
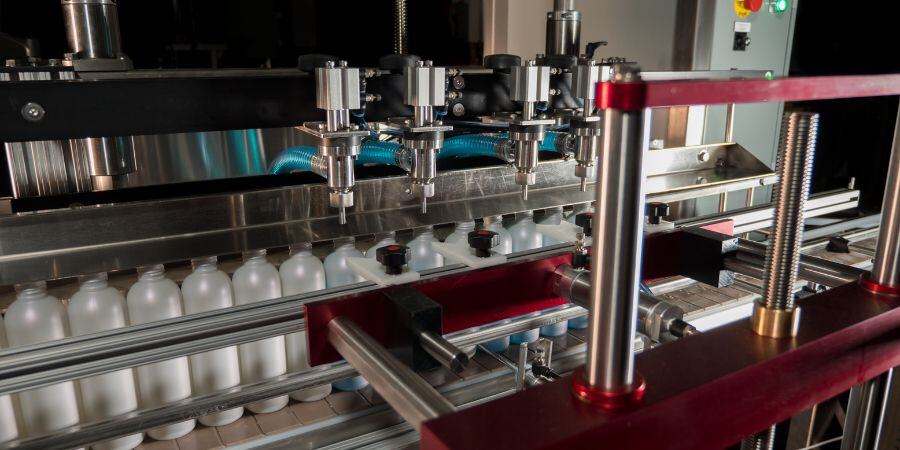
When your business is growing, it can create new challenges for you and your employees as you work to address the growing demand for your products. One way to speed up the production process is by adding a filling machine to your line!
A liquid filling machine is part of an automated production line. The machinery is used to fill products with varying liquid viscosities into containers through volumetric or quantitative filling. Liquid-filling machines can handle everything from thin, water-like liquids to heavy, viscous, and extremely thick varieties. There are also filling machines that fill containers with solids like powders or granules, but today, we’ll be discussing liquid-filling machines only. However, it’s crucial to select the right type of liquid-filling machine for your industry. Do you need a gravity liquid filling machine? A piston, pump, or overflow filling machine? We’ll help you understand.
This article is your comprehensive guide to everything you need to know about liquid filling machines, what kinds there are, what kind of liquid filling machine would be best for you, and more.
Types of Liquid Filling Machines
There are at least four common types of liquid filling machines used in production lines. They are gravity filling machines, piston filling machines, pump filling machines, and overflow filling machines.
Gravity Filling Machines
Gravity filling machines, expectedly, use gravity to fill containers with liquids. A raised tank on this type of bottle filler retains product until containers are placed under the fill nozzles. The valves on the fill heads or nozzles then open and release the product for a predetermined period. Each fill head may be separately timed, ensuring a precise volumetric fill for each bottle. Gravity filling devices, including automated and semi-automatic liquid fillers, are ideal for free-flowing, low-viscosity materials such as water, oil and ink. Special gravity filler nozzles may also be used to avoid drips and regulate foaming in particular materials.
Advantages and Limitations of Gravity Filling Machines
Gravity-based liquid filling machines are simple and cost-effective. However, gravity filling machines may not be suitable for handling high viscosity products effectively..
Piston Filling Machines
Piston-based filling machines can be semi-automatic or automatic, depending on your needs. In the process, a tank of product is opened, and the piston rotates, drawing the product into the piston filler cylinder. The tank head closes while a fill head opens. The piston rotates again, pushing the product through the fill head into the container, and the process starts over.
The cylinder diameter and piston stroke length determine the volume of each fill. Adjusting the piston stroke changes the fill volume. The piston pulls the product into the cylinder and then forces it into the supply line. Proximity switches ensure correct piston movement.
Semi-automatic piston filling machines can be designed to convert to automatic machinery, allowing for future upgrades. Alternatively, semi-automatic fillers can be built as tabletop machinery. Whether you are looking to enhance the efficiency of an existing packaging line or start packaging new products, piston fillers offer the versatility to be the ideal filling machine for a wide range of projects, from cosmetics to pharmaceuticals.
Advantages and Limitations of Piston Filling Machines
Piston filling is fast and precise and reduces product waste. However, by definition, these filling machines are more complex and require more parts than gravity fillers. It requires more skill to operate a piston filler. Piston fillers are also more likely to cause shear or a kind of stress between the piston and the liquid being put into the packaging.
Overflow Filling Machines
Overflow filling machines operate with a two-part nozzle. The first part of the process starts when the supply side of the nozzle pumps your product into the container to the target fill height. The second part of the process starts here. As the target height is reached, any excess product or foam are pumped back to the original source container through the second part of the nozzle. Overflow filling machines are ideal for sauces and syrups, as well as non-food liquids like gels, foaming cleaners, chemicals, and more.
Advantages and Limitations of Overflow Filling Machines
Overflow filling machines fill every container to the same level, creating a polished and uniform look for your product. This kind of filling machine is able to consistently fill lots of different bottle shapes and sizes as well. Overflow filling machines are not ideal for particularly viscous materials or extremely large containers, however.
Pump Filling Machines
Pump fillers use a pump to draw product from a drum and deposit it into the container. Pump fillers typically measure the fill volume by counting the number of gear revolutions in a process called pulse timing. Another method is time-based filling, which involves pumping the product for a set amount of time, although this is generally less accurate than pulse timing.
Gear or lobe pumps use positive displacement to pull liquid through their moving components. Pump filling is ideal for greater viscosity liquids and particles since the fluid does not clog the moving components as quickly as in other types of filling machines.
Peristaltic pumps employ flexible tubes and rollers to entirely isolate the pump's moving components from the product, making them suitable for delicate liquids such as medications or flavored liquids, as well as extremely corrosive or dangerous liquids. After each manufacturing run, the tubes are readily changed, ensuring that the system remains perfectly hygienic for the next run.
Pump filling machines are great for several different industries, including food, pharmaceuticals, and cosmetics.
Advantages and Limitations of Pump Filling Machines
Pump filling systems are quick, making them useful for large containers where accuracy is less critical. Other types of pumps use lobes or peristaltic action, squeezing rubber tubes to control product flow.
Unlocking Efficiency: Key Considerations for Choosing the Right Filling Machine
When selecting the optimal filling machine, several crucial factors must be carefully weighed to ensure efficiency, precision, and cost-effectiveness in production processes. First, the production volume and speed requirements serve as fundamental benchmarks, dictating the necessary throughput capacity of the filling equipment. Matching the machine's capabilities with the demand ensures smooth operations and prevents bottlenecks.
Equally critical is understanding the type of liquid being filled and its viscosity, as this determines the appropriate technology and mechanisms needed to maintain accuracy and consistency. Furthermore, consideration of container size and shape is pivotal, as it directly influences compatibility and adaptability with the chosen filling equipment. Whether dealing with bottles, cans, or pouches, selecting a machine that accommodates the specific dimensions and characteristics of the containers is essential for optimal performance.
Integration capabilities with existing production lines and automation systems also play a pivotal role in streamlining operations and enhancing overall efficiency. Investing in equipment that seamlessly integrates with other machinery minimizes downtime and maximizes productivity. Additionally, budget and cost considerations are significant determinants in the decision-making process, as they affect the feasibility and long-term sustainability of the investment. Striking a balance between upfront costs and potential long-term savings through increased productivity and reduced waste is essential for making an informed decision.
By carefully evaluating these considerations, businesses can select the right filling machine that aligns with their production needs, liquid properties, container specifications, automation requirements, and budget constraints, ultimately optimizing their manufacturing processes and ensuring competitive advantage in the market.
Find the Right Liquid Filling Machine for You with Apex Filling Systems
The process of selecting the ideal liquid filling machine for your production line is a multilayered endeavor that requires careful consideration of various factors. Understanding the functionalities and industry suitability of different types of filling machines is paramount to making an informed decision. Whether your product necessitates a volumetric filler, piston filler, or gravity filler, each option presents its own set of advantages and limitations. By weighing the pros and cons against the specific needs of your operation, you can effectively optimize your liquid filling processes to enhance efficiency and productivity.
Remember, the versatility of liquid-filling machines allows them to handle a broad spectrum of liquids from thin and watery to thick and viscous. However, nuances such as foaminess, shear sensitivity, and other specifications may sway your choice toward one type of filling machine over another. Ultimately, by carefully considering these factors and conducting thorough research, businesses can confidently invest in the right filling equipment, paving the way for streamlined operations and sustained success in their respective industries.
Request a consultation today to optimize your production line efficiently. Our team is here to provide expert guidance and support every step of the way, ensuring a seamless and successful integration of the chosen equipment.
Share this
- Help First (78)
- Filling Equipment (32)
- Informational (29)
- Apex Filling Systems (25)
- Industry Insights (25)
- Automatic Filling Machine (23)
- About Apex (19)
- Packaging Equipment (18)
- Apex Filling (10)
- Automatic Capping (10)
- Fillers (10)
- Apex (7)
- Uncategorized (5)
- American Made Goods (3)
- Apex Family (2)
- Absolute Truth (1)
- Apex Team (1)
- Apex Way (1)
- Petroleum (1)
- oil (1)
- April 2025 (5)
- March 2025 (10)
- February 2025 (12)
- January 2025 (14)
- December 2024 (1)
- November 2024 (4)
- October 2024 (4)
- September 2024 (2)
- August 2024 (1)
- July 2024 (4)
- October 2022 (1)
- September 2022 (1)
- June 2022 (1)
- October 2021 (2)
- June 2021 (1)
- May 2021 (1)
- April 2021 (2)
- March 2021 (2)
- February 2021 (1)
- January 2021 (2)
- November 2020 (1)
- October 2020 (1)
- September 2020 (2)
- August 2020 (1)
- July 2020 (1)
- June 2020 (1)
- May 2020 (1)
- April 2020 (2)
- March 2020 (2)
- February 2020 (2)
- January 2020 (3)
- December 2019 (2)
- November 2019 (6)
- October 2019 (4)
- September 2019 (3)
- August 2019 (6)
- July 2019 (2)
- April 2019 (1)
- February 2019 (1)
- January 2019 (7)
- December 2018 (6)
- November 2018 (5)
- October 2018 (2)
- September 2018 (2)
- August 2018 (1)
- July 2018 (3)
- May 2018 (2)
- April 2018 (1)
- March 2018 (2)
- February 2018 (2)
- January 2018 (2)